In today’s machining environment with high part mix and varying batch sizes, cutting tool demand is larger than ever. Tools cause a major bottleneck, driving up costs and limiting overall productivity. In this blog, we share ideas on how to solve the typical tool-related bottlenecks in milling machining.
When tool changes are frequent and the number of needed tools is higher than number of pots in the magazine, you typically have a problem. Operators need to input a new set of tools often – while your machine tool sits idle. This leads to extended setup times and lower spindle utilization – not to mention the delays in other tasks the operator is needed for.
If you run parallel machining centers, what is your strategy to ensure sufficient tooling? Purchasing the largest possible tool magazines and dedicated set of tools for each machine is a large investment that also adds more duties to operators.
Then there’s quality. Manual tool data input is a frequent source of errors. If your operator types 30 digits of tool data 30 times per day, there are 900 possibilities for a false input every day. You need a superhero to avoid fat-finger errors! Tool loading errors result in quality issues, higher scrap rates, and time-consuming rework. All of this drives up production costs and eats into profits.
This is where tool automation steps in.
What’s Tool Automation?
Tool automation is a system designed to reduce idle time and improve quality in machining environments with large number of tools. It can either be a stand-alone system or a part of flexible CNC automation system.
Here’s what a tool automation system consists of:
- Centralized tool storage – accommodates large number of tools centrally so that each tool can be used by any parallel machine tool.
- Transfer device, typically a robot – delivers tools between machining centers, centralized storage, and tool maintenance.
- Operator interface – place where the system brings worn-out tools for operators to take them to reworking – and other way around.
- Software – plans tool deliveries based on machining schedule, guides operators work on which tools to preset by when and optimizes tooling for maximum spindle utilization.
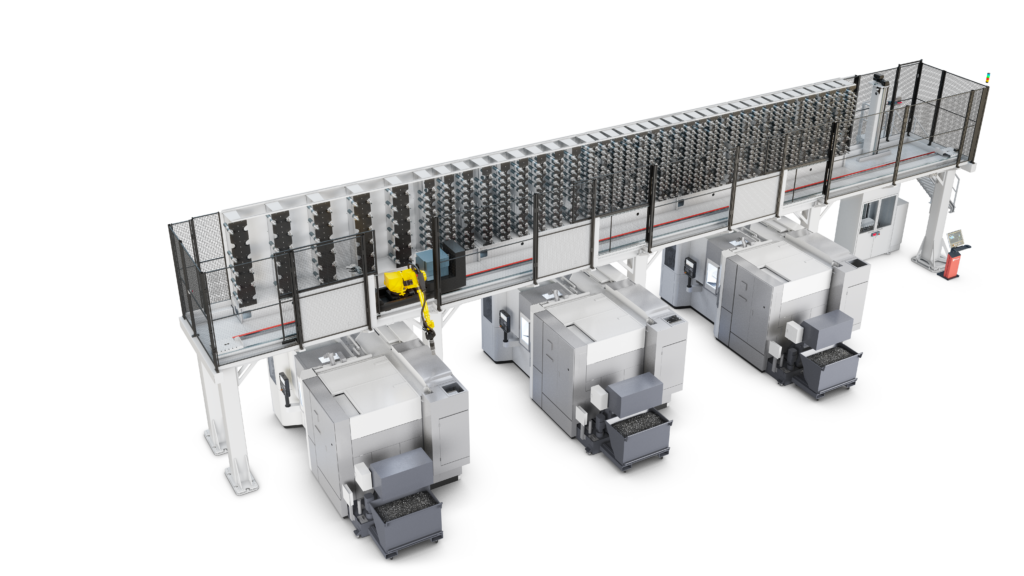
Why Does Tool Automation Make Sense?
Tool automation system ensures automated tool sharing, timely tool processes and automated tool data transfer. This results in higher spindle utilization, full tool availability, error-free operation, as well as minimized cutting tool and tool magazine investments. Here is how tool automation runs your tool processes:
- Optimizing Your Tool Investment – Tool automation tracks your tool data: nominal life, cutting time left, NC-programs using the tool, sister tools, presets, and more. The data is used to help you optimize your tool set: it tells if you could achieve higher spindle utilization by adding more sister tools – and on the other hand reduces waste by reporting the tools that are not used at all.
- Schedule Your Tools for Maximum Spindle Utilization – Tool automation plans tool usage up to 96 hours ahead, based on your production orders and tool availability. Tools are delivered to machines just in time, meaning that the NC-program can begin even though some of the tools needed later are still used by other machines.
- Maintain Your Tools Timely and Without Errors– Once a tool does not have enough life left for the next machining job, it is automatically delivered to the operator area for reworking. Your operators are provided with a list showing which tools to preset by when. When a tool is preset, tool data transfers automatically. Your operator only needs to take the physical tools back to one centralized tool station.
- Use Your Data for Development – Tool automation gives full visibility on your tools and their history. To begin with, you know exactly where your tools are. There are also optimizations that improve productivity – for example, tool automation can track recurring events such as tool breakages with a certain machine tool or an NC-program – advising you to make optimizations on machining.
Did You Know?
With flexible tool automation, you don’t need to have every tool in the magazine to begin your NC-program. Tool automation brings in tools as they are needed. This means for example that another machine can still use tool #14 when your program begins, and you can count to your tool automation to bring in the tool by the time it’s needed.
Cutting tools play a key role in manufacturing efficiency – making it equally important process to streamline as workpiece or pallet changing. Fastems has automated cutting tools for 28 years and we have witnessed manufacturers achieving 90+ percent spindle utilization by integrating tool automation. Go ahead and explore tool automation – to see real-life examples on how others have done it, check out this page.
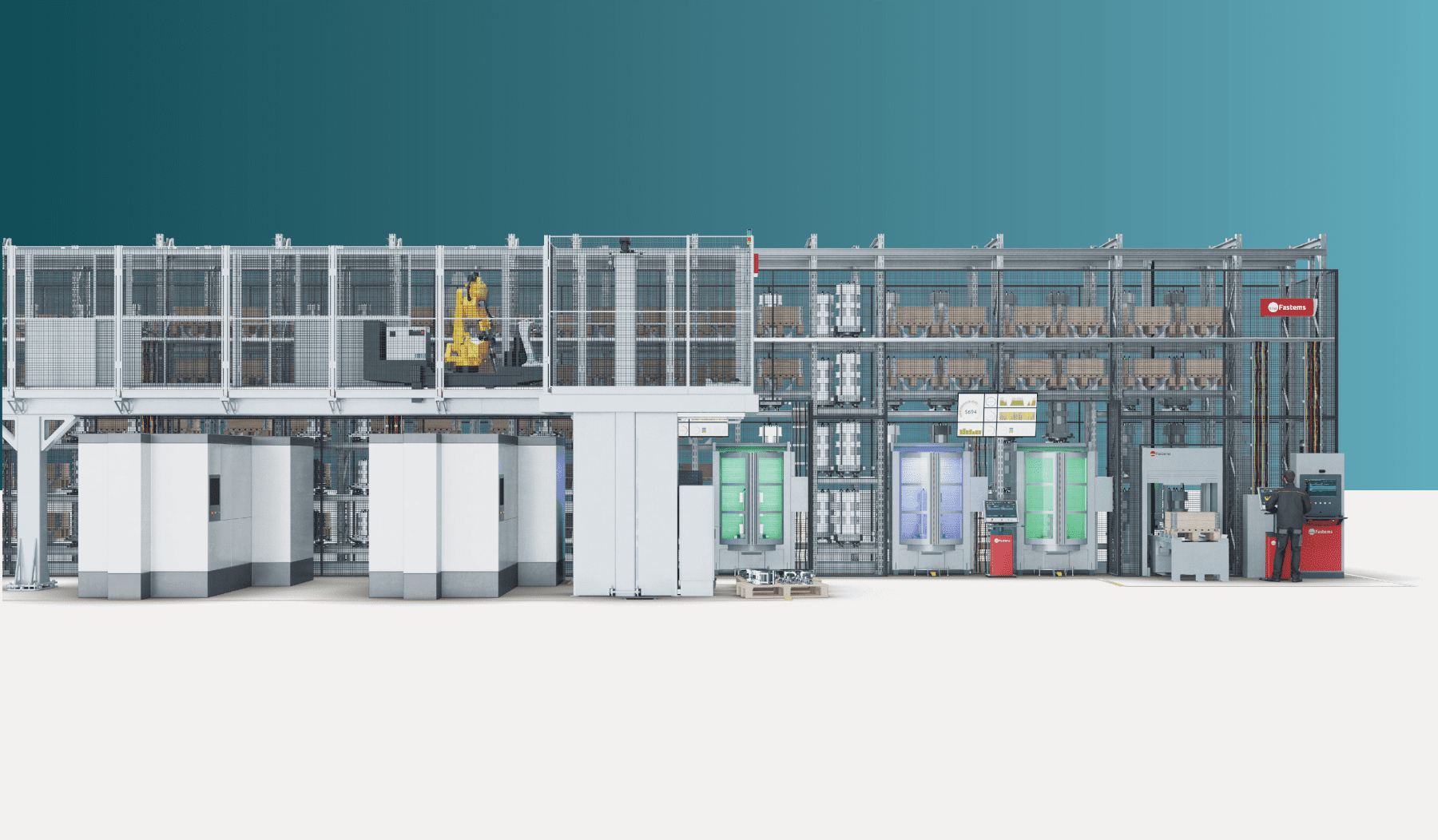
Are you joining EMO in Hanover 2025?
Visit Fastems in Hall 12, Booth B54. We’ll show you how tool automation could look like on your shop floor, featuring either our CTS (Central Tool Storage) or GTS (Gantry Tool Storage) tool automation systems.
Want a free ticket? We have it ready for you — just click the button and join us!
To read more about Fastems’ Automate Machining and More showcase, check our event page.