On March 25th, a two-phased high-end flexible manufacturing system (FMS) agreement between Suzhou New Hongji Precision and Fastems was signed and entered into force.
The cooperation is hoped to further strengthen the intelligent manufacturing capacity and leadership of New Hongji in the Chinese machining industry. According to the news release from Fastems (Shanghai) Co., Ltd., the collaboration will also take Fastems’ Chinese business operations to the next level.
Located in Suzhou, China, New Hongji Precision is a typical High-Mix, Small-Batch manufacturing company. The company is specialized in the manufacturing of customized precision parts for the medical industry, including optical and general industrial products. New Hongji is focused on business innovations and smart manufacturing. The management team’s sights are set on improving automatic order scheduling, tool automation and automated monitoring processes.
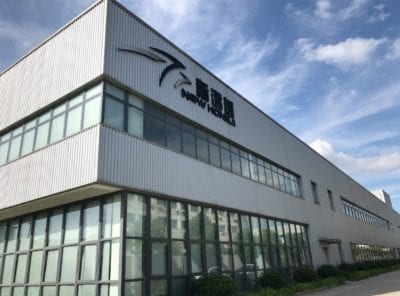
Entering into the future of manufacturing with Fastems MLS
“We had lots of discussions about FMS and focused on visualizing what the future manufacturing will look like. Along the way, we also talked about another hot topic: tool automation,” explains Robert Ding from Fastems (Shanghai) Co., Ltd. “Once this Fastems MLS is up and running, New Hongji will be able to implement lights-off production periods of up to 24 hours at a time.”
Two 4 axis HMCs and four 5 axis machining centers will be integrated into the Fastems MLS – Multi Level System on the New Hongji factory floor. The system is equipped with a high capacity vertical storage rack with over 200 pallet storage places for machining and material pallets. A highly efficient stacker crane that operates at 150m/minute running speed is used for the pallet transfers. The MLS is controlled by Fastems MMS – the most Intelligent manufacturing management system in the industry.
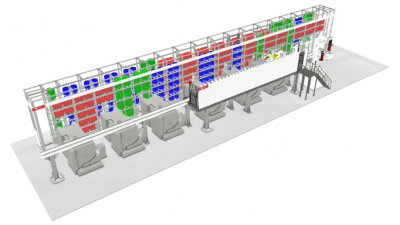
Minimizing human error and saving floor space
All the pallets, fixtures, raw material, and WIP are stored in the system’s rack. This allows for automatic transfer to loading stations and machining centers for production, according to the manufacturing orders issued by Fastems MMS. By doing so, human error is minimized and levels of productivity and safety on the factory floor increase.
One thousand tools inside the Gantry Tool Storage – GTS will be the key to push New Hongji’s productivity to the next level. The GTS will be built on top of the machining centers saving floor space and allowing New Hongji to get the most out of their factory floor. Thanks to the GTS, the built-in tool storage in the machining centers can also be minimized.
Tool Management
“Tool management has been the most tricky issue for us. In the GTS however, automatic tool transfers and real-time tool management is possible, which helps us minimize human error,” explains Mr. Jian Li – General Manager of New Hongji Precision Parts (Suzhou) Co.
“Our target is to achieve no less than 92% machine utilization with the FMS and GTS provided by Fastems.”
The GTS robot will handle tool management. This means tools and tool information will be transferred automatically to the designated machining centers as needed. Tools can be shared between machines, which means that the need for sister tools decreases and tool lifetimes become maximal. A chip will be inserted into every single tool to allow for automatic tool information transfers.
Flexible Manufacturing – The key to improving productivity
“Needless to say, automation is the way to stand out from fierce competition. Many cases have proved that the introduction of an FMS is the key to improve the productivity and internal management of a company,” continues Li. “We are confident in Fastems’ capabilities as a provider. With their experience and customized services we hope to increase our production capacity and management ability to an international level”.
“In the near future, we’ll implement a second FMS. This will be linked to the first by the means of a shuttle robot, making the sharing of tools between systems possible,” explains Li.
“The delivery of high-end Chinese manufacturing quality depends on innovative companies like Suzhou New Hongji. Forward thinking, courage and an international vision,” sums up Ding. “This cooperation with New Hongji will make Fastems more confident in its ability to contribute to intelligent manufacturing in China. From design to implementation to a complete solution. Everything from hardware to software, we are ready to accelerate the growth of intelligent manufacturing in China.”
The original article was in Chinese and published in the official Fastems China WeChat channel: https://mp.weixin.qq.com/fastems china- newhongji