The fourth industrial revolution and rising demand for Digital Twins is bringing Fastems’ offering into the virtual world, introducing unique possibilities for universities and other educational establishments. Specifically, Fastems has introduced Digital Manufacturing solutions as a platform for training, education and research activities. The goal of these virtual systems is to bring manufacturing into classrooms and create an interactive learning environment. In addition, they enable students to learn by doing and won’t require any actual manufacturing hardware.
Digital Manufacturing solutions consist of two main options: local and cloud installations. The cloud-based solution can be used with just a web browser and internet access and is a really easy way to demonstrate flexible manufacturing. The more powerful solution is the local installation. This option includes a physical cell controller and the ability to utilize Visual Components for simulating production activities. Both versions come with the required support material to get you started and ready to operate just like a real manufacturing system would.
If we haven’t convinced you quite yet, be sure to keep reading to see how Tampere University (TAU) has utilized their Virtual FMS and how the process of creating the learning environment went.
A Growing Need for Virtual FMS
The first-ever Virtual FMS was delivered to TAU at the beginning of June 2018 and was first utilized as a learning environment in the winter of 2019. Fastems and TAU have always had maintained a close relationship because of the multiple research projects they have completed together and because a large part of Fastems’ employees come from the university. TAU is also part of the Training Center consortium and has utilized the Fastems Training Center, our FMS learning facility located in Tampere, and its small FMS for their education previously and has utilized the Fastems Training Center and its small FMS for their education previously.
Although a fantastic learning facility, the problem with the Training Center is was that a large part of the available time is spent getting familiar with the system. As stated on the TAU website, “the challenge of education related to large technical systems is to provide enough hands-on experience. Virtual models and visualizations make it easier to explain the behavior of those systems.”
In sum, this means that with the help of the Virtual FMS, students can be introduced to manufacturing in an interactive virtual learning environment beforehand, and later spend their time in the Training Center actually using the real system. Just like with real manufacturing systems, the basic principles of manufacturing will be learned with the Virtual FMS first, and can then be applied at the Training Center. Through this, students can have a much more gradual learning curve and are able to grasp the fundamental concepts of manufacturing much easier.
Simulate Reliability, Performance and Flexibility with the Visual Components Model
The heart of the Virtual FMS is located inside the StationCommander-device, which hosts the Manufacturing Management Software (MMS) and enables all manufacturing activities that are carried out with the system. It is the interface (human-machine interface, HMI) between the operators and the hardware. The StationCommander can then be connected to other devices, such as screens, to easily showcase what’s going on with the manufacturing system and what the operator is doing. Additional PCs can also be attached to enable the simultaneous use of the MMS.
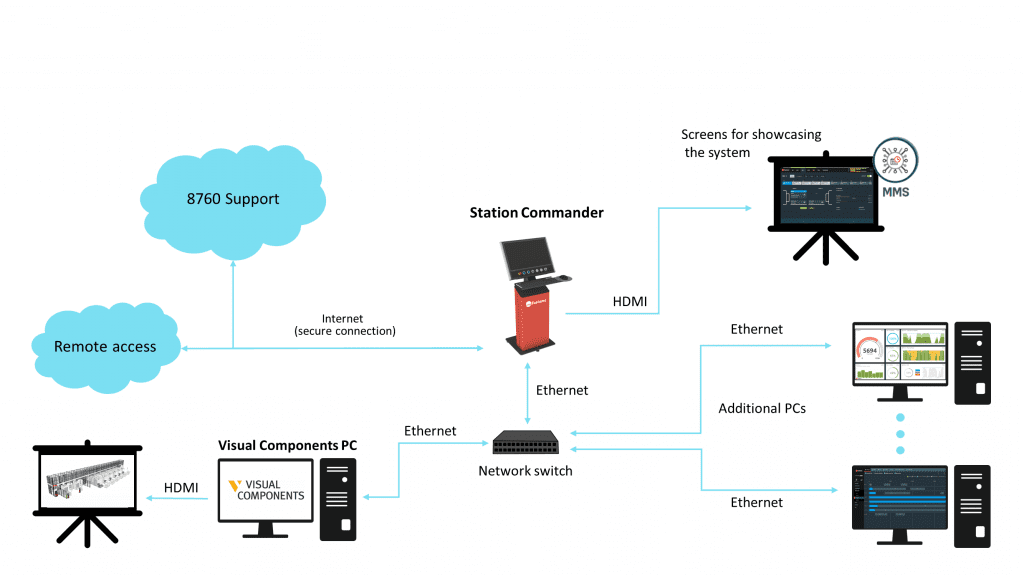
Figure 1. System architecture
A key part of the Virtual FMS is the addition of a Visual Components model. The model acts as the manufacturing hardware of the virtual system and is capable of detailed simulation activities. This allows you to experience and showcase the reliability, performance and flexibility of your virtual system. The model is connected to the MMS and is able to run the production in real-time, which makes displaying the different manufacturing activities easy. Visual Components also has VR support, which allows you to jump into your own virtual factory and experience everything first-hand directly from the factory floor.
The road from delivery to teaching
The process of creating the learning environment stemmed from a demand for bringing manufacturing into classrooms. TAU found the Virtual FMS to be a perfect platform for their needs and decided to build their learning environment around it.
After the system was delivered and installed, employees were trained to use MMS and all of its features. They were then able to start diving deeper into the virtual system and explore its capabilities. Because there are so many possible uses for our virtual systems, our customers have the opportunity to create just about any exercises they want. This allows them to tailor the exercises and other activities for their own needs and capabilities.
Creating the Exercise Structure
A few weeks after the system delivery, TAU started to create the exercise structure for their upcoming Introduction to Production Engineering -course. The exercises were designed in a way in which each exercise relied on the information learned in previous exercises and lectures. This way students could build their knowledge gradually and weren’t overwhelmed by new information. Before having introduced the virtual system to the course, students had to visit the Training Center without any prior practical experience with manufacturing systems. This made learning at the Training Center rather difficult because students had a massive amount of material to learn in a short period of time.
TAU decided to create four exercises and supported them with a few lectures to give the students a great overview of manufacturing. The exercises started with an introduction into the MMS and then gradually started to ramp-up in complexity. During the second and third exercises, students learned the basic principles of flexible manufacturing and the process of manufacturing parts using both the Virtual FMS and a real FMS. Then, the purpose of the final exercise was to tie everything together and required the students to actually think about the important aspects of manufacturing. They learned to think about which KPIs are important for different target groups. For example, the CEO might not be as interested in the day-to-day operation of the system as the production worker is. The students were able to pinpoint the needs of different company players through their experience with the different aspects of manufacturing – they had gone from shop floor to top floor.
By the end of the course, the students had a great understanding of flexible manufacturing. They learned the basic workflow of the factory floor and were then able to apply their knowledge to find the key performance indicators for each target group. Overall, they had a comprehensive introduction to manufacturing and are now able to start developing a deeper understanding of the subject.
If you want to learn more about the exercises, please check out this article.
What’s to come?
The feedback from the students after the course was highly positive and everyone was enthusiastic about introducing the Virtual FMS to other courses as well. TAUs plan is to keep the Virtual FMS as an integral part of the Introduction to Production Engineering -course and to also utilize its simulation and Virtual Reality capabilities in other courses. This way, students can keep developing their skills gradually and won’t be overwhelmed with new information and TAU can still utilize all of the amazing features of the Virtual FMS.
TAU is also interested in teaching and researching topics related to Data Analytics and Digital Twins, making their Virtual FMS a great platform for this because of how it simulates a realistic production environment and can, therefore, produce a massive amount of interesting data.
For more information about the TAU Virtual FMS, please head to: https://research.tuni.fi/virtualfms/