Do you want to improve the return of your CNC investment? Great – this blog series is for you. During the past 40 years we have witnessed thousands of successful CNC investments – and many that could have paid off much better. This post focuses on production philosophies: typically the CNC investment is specified to a certain job which often doesn’t make sense. Read and learn why!
Get rid of ‘1-man-1-machine’ production philosophy and make more profit
The most typical driver for CNC investment is a new production need: you need to produce more of your existing parts, or have new parts to manufacture. When you purchase a new machining center, you also hire a CNC machinist (for every shift) and purchase pallets, fixtures and tools for that machine. This is the typical setup in machine shops all over the world: production resources – machine tools, machinists, tools and fixtures are dedicated to certain jobs. This is what we call ‘1-man-1-machine’ production philosophy. You certainly get the extra capacity you need by adding more resources but at the same time your operating costs rise correspondingly.
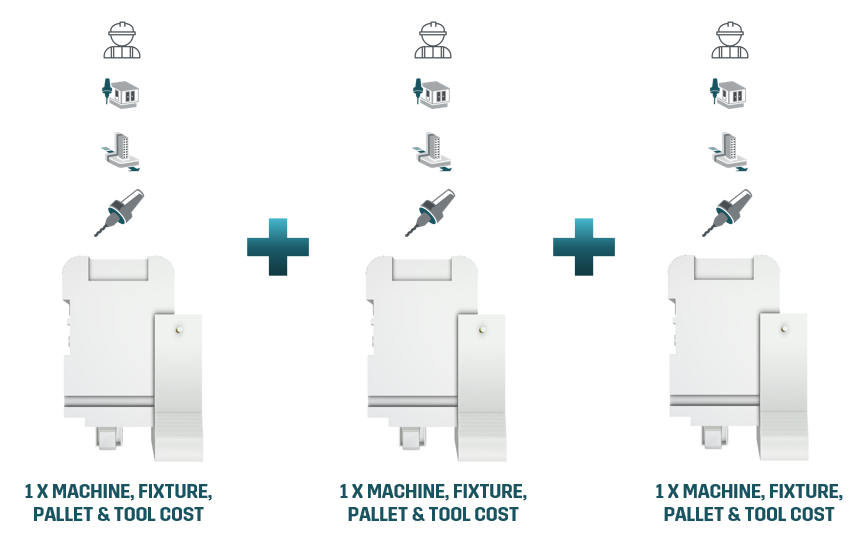
Job dedicated machining AKA ‘1-man-1-machine production’ means that machine tools, labor, pallets, fixtures and tools are dedicated for specific production jobs. The investment and operating costs rise correspondingly when new CNC capacity is added.
Flexible production: what does it mean and why it makes sense?
Flexible production means sharing the CNCs and other production resources between the jobs. Based on the current production need, every resource and machine are dedicated to what is needed to produce at that moment. Shortly: ANY machine (with the right capabilities) can machine ANY job. When all of your CNCs can produce any part, you can utilize your machining capacity even if different parts have differing demands. On the other hand, when some of your CNCs is out of use for a period of time (maintenance, machining break), you can still produce your whole production mix.
Flexible production requires flexible automation – automation that has full visibility on your production orders and is capable of sharing the production data of each job (NC programs, tool data, fixtures, pallets) to your CNC machines. An automation that can store enough pallets and fixtures for your production mix – and schedule all jobs between your machines so that (1) the overall machining capacity is maximally utilized, (2) every single job will be ready on time, and (3) minimal amount of production resources are needed.
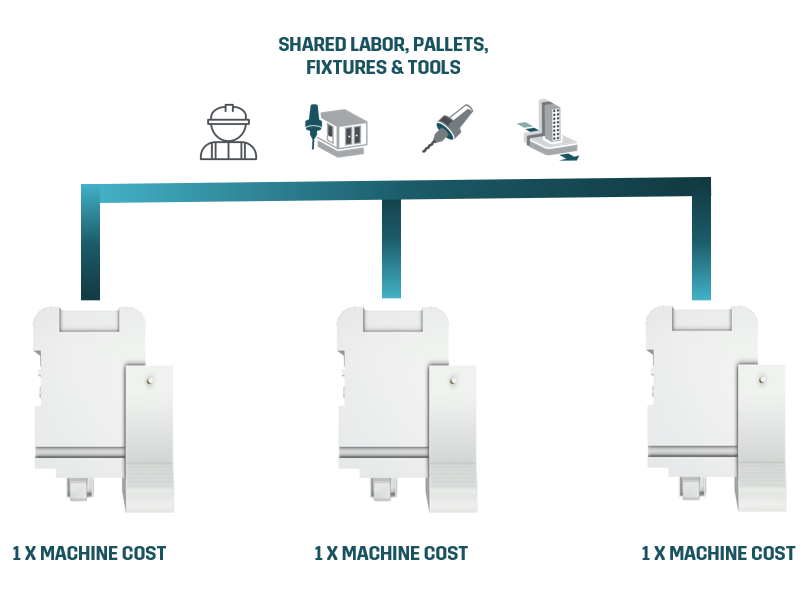
With flexible automation all jobs are shared between the machine tools that are capable of running those jobs. The production resources: labor, pallets, fixtures and tools, are shared between the CNC machines – meaning that less pallets, fixtures and tools are needed, and one operator can take care of multiple CNC machines, ultimately reducing cost per part.
Top 5 benefits of flexible automation & how to get there
1. Minimize your CNC technology investment – Don’t settle for low machine utilization. Expect at least 70% and purchase only the amount of machine tools you REALLY need. Plan your production resource investment (pallets, fixtures, tools) so that you can share your resources between machines and generate large enough pallet storage to make sure your machines run also during lights-out periods like nights and weekends.
Exercise:
- Calculate how many machining hours (=spindle runtime) do you need in a year to produce the needed parts.
- Then calculate what was your current machining capacity if all of your CNCs ran 70% of time (6132 out of 8760 hours a year).
- Based on this calculation, how many new CNCs do you really need? Is there room for improvement with the existing ones?
2. Reduce the cost per part – When the jobs and production resources are shared between your CNCs and each operator has time to take care of multiple machines, your operating costs are lower -> reducing the cost per part. Flexible automation also minimizes the machine tool idle times (read this post about idle times), allowing for higher machine utilization. You can basically unleash the hidden capacity of your production resources, which improves your profitability.
3. Find and keep talents – Operating a machine tool requires a variety of skills including the NC programming, machine setup and tool management, not to mention that it is also physically demanding, repetitive and heavy work. Talented CNC machinists are worth of gold today and finding enough of them for ‘1-man-1-machine’ production is rather difficult since everyone needs to master everything.
Flexible automation enables skill-sharing: you can hire specialists that take care of a certain process in your machine shop instead of operating a single machine. For example, you can have an NC programmer, an automation system operator, a tool operator, and other specialists taking care of their own specialty on shop floor level.
Operating an automated production is very ergonomic and allows employees to plan their work in advance, improving overall work satisfaction. The automation system takes care of the most physically demanding transfers, and ergonomic loading stations ensure comfortable work when the operators are needed. Operators work becomes predictive when the system tells what exactly is going to happen withing the next days and months. Freedom to plan and schedule own work and being able to sleep well during nights – this is the typical positive feedback from the automated system operators.
Did you know? The majority of automation investments don’t lead to reduced head count – the profitability typically comes from reduced cost per part, being able to produce more with current resources and compete better in the markets.
4. Ensure scalability in market fluctuations – When the demand fluctuates, being capable of scaling production up and down fast is vital. A non-automated machine requires constant attention for spindle to run – basically meaning that ‘scale down’ means ‘shut the machine’ and ‘scale up’ means ‘buy a new machine and hire new people’. In automated production you always use your capacity at fullest – meaning that if you needed to produce less, you can just work shorter shifts than usual. When you need more capacity again, you can return your shifts back to normal. Resilience in market fluctuations isn’t something you necessarily calculate in the investment phase, but it definitely helps you remain profitable with whatever comes.
5. Adapt to changes and keep your spindles running – When there is a sudden change such as your machine tool breaks, raw materials are late, an urgent customer order comes – you name it – what do you do? Will you get the important jobs ready on time? Flexible automation re-schedules your production real-time when the unexpected happens. Since your automation system has visibility over your order backlog and your available production resources, it is always capable of prioritizing the production so that the most important jobs to be delivered on time.
We know – transforming your production philosophy is easier said than done. After witnessing thousands of successful transformations, we however know it is well worth the effort. If you want to learn more, download our CNC milling machine automation guide or book a free consultation!
In case you want to read more on profitable CNC investments, read our other blogs:
Make More with Your CNCs – Maximize Spindle Utilization
Make More with Your CNCs – Make Your Machining Process Reproducible (coming soon)
Make More with Your CNCs – Lower Unit Cost in High-Mix-Low-Volume Production (coming soon)