Do you want to improve the return of your CNC investment? Great – this blog series is for you!
The modern 4 and 5 axis machine technologies are extremely powerful but expensive, aren’t they? Justifying the investment might be challenging compared to (much cheaper) 3-axis machines that could basically do the job. Can you keep your powerful 4 or 5 axis machine fed, or does your machine need to stop and wait for production preparations, re-clamps between the OPs, and tool service? Do you face labor challenges – can you scale your operations easily when the demand changes? Is your new machine dedicated to certain jobs or can it support your changing production needs in long term?
In this blog series we dive into the world of CNC investments. During the past 40 years we have witnessed thousands of successful ones – and many that could have paid off much better. Here are the best practices to get the most out of your machine investment, starting with the obvious one – increasing machine spindle utilization.
Talk with CNC automation specialist Download milling machine automation guide
How to Maximize CNC Spindle Utilization
An average machine shop can utilize 20-30 percent of their machining capacity (=time when the spindle runs). This is mainly because the CNC machines are constantly waiting for something else to be done, whether it is preparations for the next batch, an operator to load tools, or someone to re-clamp the part for the next operation (OP). Basically, most of the machine tools need constant supervision to be somewhat productive – and even then, the machine waiting times form a significant capacity loss in the long run. As long as machining and operator cycles are not in perfect harmony, the machine waits.
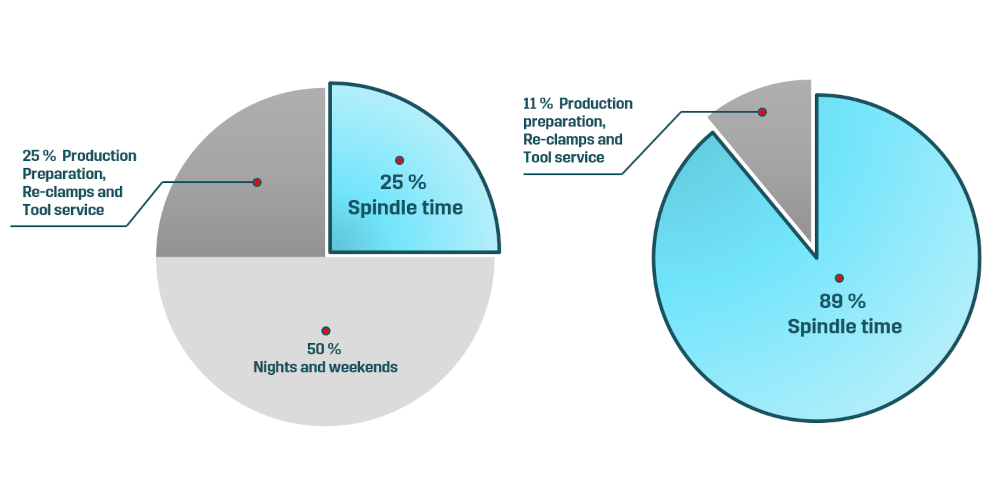
Spindle utilization: the modern 4 and 5 axis machining centers are extremely powerful but expensive. The more your machine runs, the more profit you make with your CNC investment. The left-hand pie represents 80% of machine shops – which pie represents your shop better?
Here are the Fastems tips on how to optimize the three main idle time causers of your shop floor:
1. Minimize your idle during the machining preparation times
Production preparation is typically the most time-consuming part in CNC machining. You need to measure and load the tools, bring raw materials, build fixtures, input the NC program into the machine, make first cut(s) to adjust everything for precise results – this process can take hours, sometimes even days. If your machine tool is waiting (=spindle not running) during this process, you are losing a very significant part of your money-making capacity!
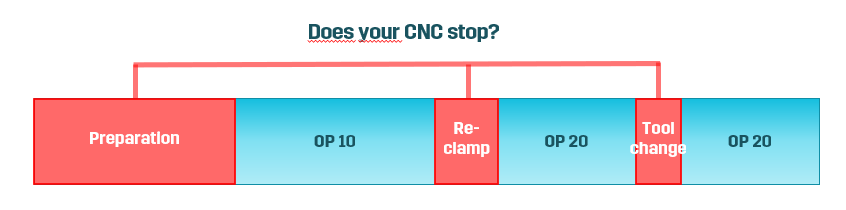
Does your CNC stop during production preparation, reclamps and tool service? Can you (1) make your CNC run during the operator intervention and (2) minimize the production setup times?
Consider:
- Prepare the next job while your machine is still running the previous work
- pallet storage + automatic pallet changer: depending on your production volume, cycle times and production mix, having a small or large automated pallet storage enables machining in parallel with production preparations. Your CNC runs unmanned for longer periods of time and stops only for seconds when the pallet is changed.
- predictive production scheduling software – with a predictive production scheduling and control software you KNOW your upcoming preparation needs and that way you can load the next jobs IN ADVANCE (raw materials, tools, NC programs, pallets and fixtures).
- Save the production setups so that you don’t need to start your recurring order preparations from scratch every time
- The production preparation consumes a lot of time. Flexible CNC automation works with pre-configured setups: having all the needed information regarding raw materials, NC programs, tools, fixtures, and work instructions stored for future use. When you have your jobs in permanent pallets and fixtures, and your NC programs centrally managed, you can start your recurring job without needing to prepare everything from scratch. With this you remove majority of manual work and save a lot of time – also by not needing to run tests since you can trust that everything happens 100% in the similar way as previously with the same job.
DID YOU KNOW? AN AVERAGE CNC MACHINE RUNS ON 20-30 % UTILIZATION, MEANING THAT OVER 6000 OUT OF 8760 YEARLY HOURS ARE LOST.
2. Loading OP10, reloading OP20, loading the next batch – rethink your loading and re-clamping
With 3-axis machine you need to make more re-clamps than with a 4 or 5 axis machining center – however the machining centers are so much more powerful that the machining speed is higher. Basically, this means that no matter what kind of machine tool you use, the need for often re-clamps and next job loading is always there unless your machining times are extremely long and setups extremely fast. Every time you make a re-clamp or load the next job, your machine waits. You might not consider this even a problem during the manned hours but how about when the lights are out, i.e., nights and weekends?
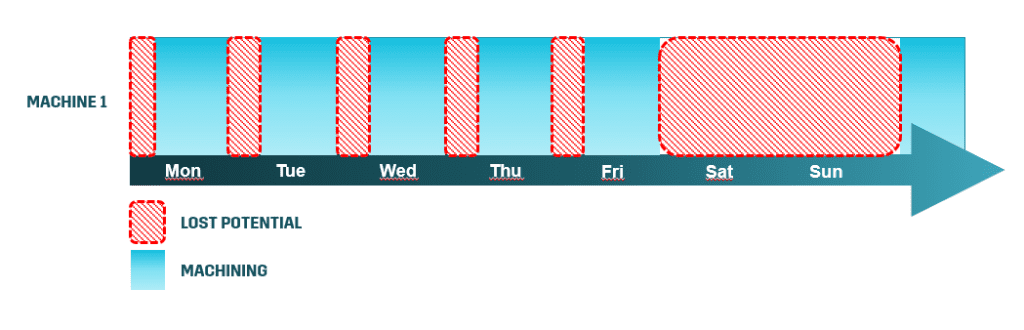
If your production requires often re-clamps or the machining cycles are not long, the unmanned capacity cannot be high without automation. For example, in a shop that operates in two shifts and is closed on weekends: if the machine could run unmanned for 2 hours and then stops for reload or re-clamping task -> 8 hours per night between Monday and Thursday, plus 56 hours each weekend would be lost. This would mean 4,160 out of 8,760 hours a year. How much more could you make with 4,160 machining hours?
Consider:
- Run a different work while you re-clamp or reload your parts
- With an automated production scheduling software and a pallet storage you can ensure that your machine is used in maximum capacity. Since the system stores all the information and resources needed to run your jobs, your machine can run its previous job while you reload or re-clamp your parts for the next one. The large enough pallet storage ensures you can run your jobs throughout the night or weekend as well.
- Automate your loading and re-clamping process
- Sometimes the need for re-clamps or loading is constant – basically meaning that even an automated machine tool couldn’t run long unmanned because the buffer is consumed so fast. Or optionally a large pallet storage would do but the required amount of pallets is so large that it becomes too big of an investment, especially when you want to run nights and weekends efficiently unmanned. Consider automatic loading. An auto-loading robot can perform your loading and re-clamping tasks and ensure the machine is utilized 24/7.
3. Make your tool service predictive
The third thing that often causes unnecessary machine tool idle are the cutting tools. Here are questions that help you spot the potential inefficiencies:
- Do you need to rework and measure your tools manually?
- Do you input the tool off-sets to the CNC control manually?
- Does your machine need to stop for tool service? How often and for how long each time?
- Is a worn-out tool a surprise or can you renew the tools in predictive manner instead of being reactive?
Especially in multi-axis machining, tools are often forming a production bottleneck. There are various tools needed for the machining operations and the tools need to be switched often because the machine tool magazine fits only a limited number of tools. It requires a lot of effort to renew and deliver the right tools to the machines timely. And if you don’t know the coming tool needs, you will need to supervise the machines ALL THE TIME to minimize idle time. The other way is to make your tool management predictive.
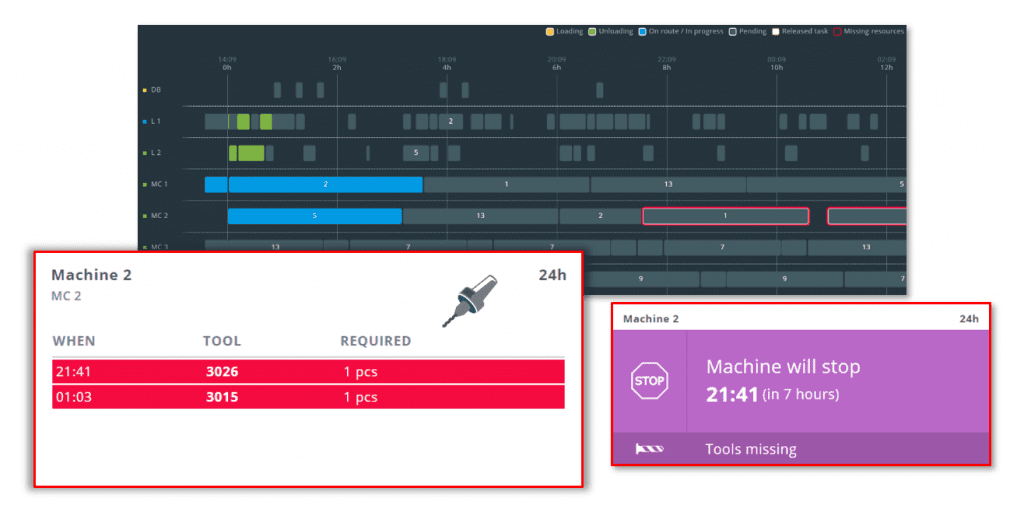
Example: Fastems Manufacturing Management Software MMS calculates the tool needs for each job and informs the operator in advance on which tools to prepare and deliver by when.
Consider:
- Make your tool management process predictive, not reactive
- Consider CNC automation that includes tool management functionality. You will know your tool needs in advance and can renew, measure, and input the tools into the machine in advance.
- Tool presetter integrated with your automated CNC production
- A tool presetter helps you minimize the tool measurement time and remove the fat-finger errors, making sure the tool data is always correct. When your tool presetter is integrated with your automated CNC machine, the data is automatically delivered to the machine tool – keeping the tool data constantly up-to-date.
- Use a central tool storage to maximize tool availability
- Large machine tool magazines allow for longer machining times without tool loading
- In very high tool demand, consider centralized tool automation systems that can store thousands of tools and manage tool transfers to/from machine tools. The tool automation systems deliver tools at the right time and to the right machine – even during machining (meaning that every tool does not need to be in the tool magazine before the machining operation starts).
- Central tool storage shares the tools between machining centers and jobs, reducing the need for sister tooling and tool magazine sizes.
- Tool life monitoring and timely rework
- Ensure you monitor tool lives automatically, so that your operators get a notification BEFOREHAND when a tool needs resetting. Otherwise, worn-out tools can cause unwanted machine stops and reduce your machining time, especially if they literally run out of life during machining.
It is simple yet complex – to do the right things at the right time, all the time. The machine idle time is just the tip of the productivity iceberg – unrepeatable machining process and 1-man-1-machine CNC strategy being two other factors pushing down CNC productivity – not to mention the manufacturers with high mix and small volumes who also need to be more competitive in their markets! Read our other blogs to learn more:
Blog 2 Make more money with your CNCs: Get rid of ‘1-man-1-machine’ production (coming soon)
Blog 3 Make more money with your CNCs: Produce small batches with lower unit cost (coming soon)
How could you get more out of your CNCs? Would you like to learn more about flexible automation technologies that enable job and resource sharing between machine tools?
Talk with CNC automation expertDownload a milling machine automation guide