Flexible manufacturing system takes care of pallet and workpiece handling – SKF manufactures bearing components in a highly automated process
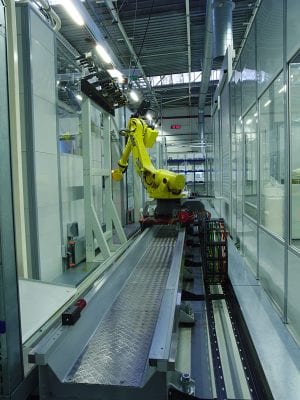
The RoboFMS from Fastems links up all the process steps required for production in a single system, handling both workpieces and pallets.
The production of small batches down to single workpieces is not something generally associated with highly automated systems – especially if the production involves complex machining, with additional, sometimes difficult process steps, and when comprehensive quality control is required.
However, SKF Aeroengine and Fastems have cooperated to create a solution that is capable of doing just that. The individual handling of workpieces and their pallets is combined in a flexible manufacturing system (FMS).
Based in Rouvignies, SKF Aeroengine France is part of SKF Aerospace and is one of five SKF subsidiaries in Europe, specializing in manufacturing bearings for the aerospace industry. With a workforce of 630 employees, SKF Aeroengine makes all kinds of rolling bearings for aircraft and helicopter engines. The company is also the center of excellence for thermal treatment of rolling bearings and roller production in Europe.
A highly-demanding, next-generation order
“About two years ago, we received an order to manufacture special roller bearing components for the new LEAP engine generation, the successor to the CFM56 engine. This order was unique for us in terms of its volume, spanning a period of 20 to 30 years, with individual batch sizes ranging from five to thirty workpieces per job”, explains Cedric Vandevoir, Process Engineering Manager at SKF Aeroengine France.
“It is a state-of-the-art turbofan engine manufactured by CFM International using the latest technologies. The machining of the complex, medium-sized rolling bearing components is very demanding, and necessitated new machining strategies and maximum precision to meet the quality requirements,” explains Marcus Jakob, Global Process Development Manager at SKF Aerospace.
Investing in performance, precision and productivity
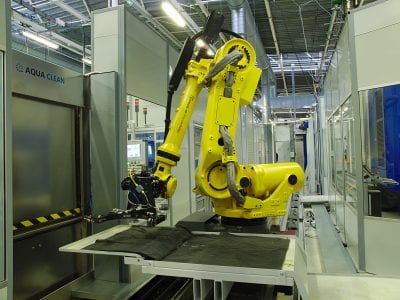
Immediately after the initial machining of the workpieces, the robot transports the semi-finished parts to the washing machine.
Given the demands for high-quality, traceable and above all economical production of small but recurring quantities over a very long time, SKF Aero had to completely rethink its existing production strategy. This was because until then, a series of manual activities were an everyday part of specific production processes. The task now was to find powerful and precise machinery for the complex production of bearing components and upgrade it with SKF expertise.
In addition, the machining – including the necessary auxiliary processes – had to be fully integrated into a single, highly productive solution. “We wanted to automate as many process steps as possible and dramatically minimize manual intervention. That’s why we started looking for partners – both for “Industry 4.0” machinery and for the automation of this ambitious project”, says Jakob.
Software expertise and experience make the difference
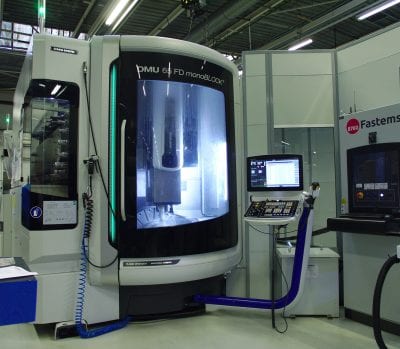
The equipment connected to the RoboFMS includes two turning/milling centers.
After a thorough review of potential system integrators, SKF Aeroengine ultimately chose Fastems; and for good reasons, as Marcus Jakob reports:
“It was important to us that our partner could respond flexibly to the very different requirements of the overall project, which will also be rolled out to other SKF Aero plants, as well as responding to individual requests. The software plays a crucial role in this. Robots are standard today and are easy to acquire.
But what’s crucial here are expertise, integration and flexible implementation in the application itself. What impressed us about Fastems was the size of the company, the number of in-house software developers and above all their expertise in flexible software solutions for automation.”
A complex complete solution including quality control
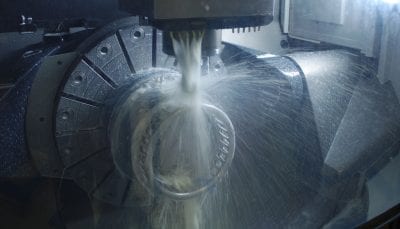
The complex workpiece geometry requires quite long machining times. For this reason, two blanks are usually machined in parallel on the two turning/milling centers.
The initial ideas from SKF Aeroengine were refined in the course of the project with Fastems to the present system known as the “RoboFMS” (Robotic Flexible Manufacturing System). “Thanks to the excellent cooperation between SKF and Fastems, we were able to quickly find new and innovative solutions and reach important milestones in the project”, says Jakob.
The machines and systems connected to the flexible manufacturing system give an impression of the complexity of the overall solution, consisting of:
- two turning/milling centers
- grinding center
- lapping machine
- 3D coordinate measuring machine
- parts cleaning system
- laser marking system
The RoboFMS also includes a loading and unloading station for automated guided vehicles (AGVs) and a storage unit for blanks, semi-finished parts and finished parts.
An FMS for highly flexible handling
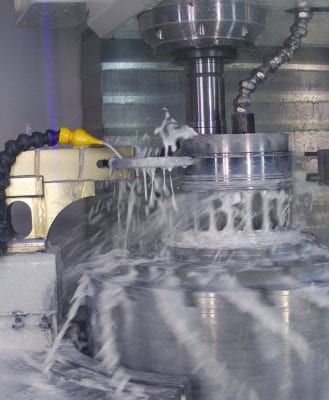
Specific machining processes such as in the grinding machine are only possible without clamping, which means the workpiece at the loading station must first be removed from the pallet so that the robot can load the machine.
The RoboFMS links up all the process steps in a single FMS: from the initial machining of the workpieces previously clamped on zero point clamping systems at the loading station to the two turning/milling centers, to processing on the lapping and grinding machine, to laser marking and quality control, taking account of the previous process steps.
The robot traveling on a rail is able to handle workpiece pallets as well as workpieces without a pallet. Vandevoir says: “For reasons of precision, the machining processes on the lapping and grinding machine can only be carried out without clamping, so at this point an employee has to unclamp the workpiece at the loading station so that the robot can first load the lapping machine and then the grinding machine with a semi-finished part.”
The timing of the transport movements in the RoboFMS determines the chronology of the overall process – and that depends on the status of the workpieces, the tools, the machines and other stations in the system. Sometimes a semi-finished part may first be placed in the system storage unit, for example, if a workpiece is already in a machine or in a measuring or marking station.
Close to zero set-up times on the machines
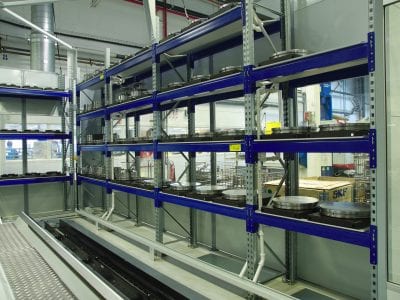
One of the integral parts of the RoboFMS is a storage unit for blanks, semi-finished parts and finished parts. If enough material is available, the system can produce autonomously for a long period of time.
Once the tools have been prepared and there is enough material in stock, the RoboFMS is designed for a high level of autonomous production over a long period of time.
“Our aim is to be able to produce for an entire weekend unmanned, even in batch sizes of 1. The prerequisite for this is that there are enough clamped workpieces and unclamped semi-finished parts in the system storage unit so that all stations in the RoboFMS can be operated at any time. We are currently working on enabling the system to produce all the rolling bearing components in a highly automated process, without manual set-up by operators”, says Jakob.
More than central planning, control and monitoring
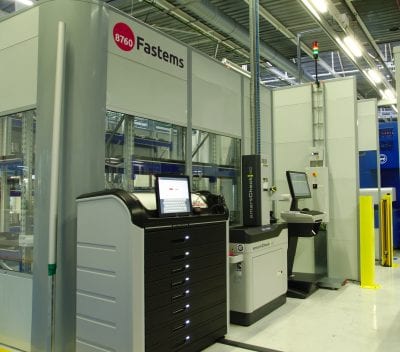
The tool check is located directly next to the RoboFMS.
One of the essential components of the project, according to Cédric Vandevoir, is the Fastems Manufacturing Management Software (MMS):
“We will soon be connecting the MMS to our ERP system so that we can directly plan production on it. The software will then also control and monitor the entire automated production.
The MMS also enables us to map the overall efficiency of the RoboFMS so that we can react quickly when required, for example by specifically optimizing individual processes. The software offers all the prerequisites for this.”
An essential part of production
The cooperation between SKF Aeroengine and Fastems can already be considered a success, as Vandevoir says:
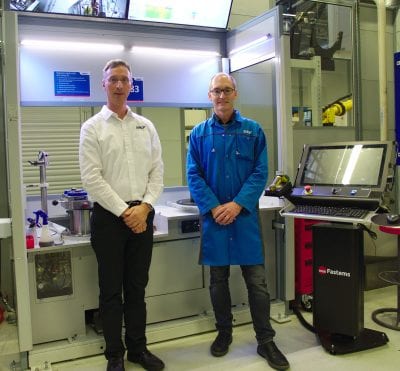
Gilles Ofcard, Factory Manager at SKF Aeroengine France (left): “As part of the change in culture, we need to show that the technology helps us to further improve our quality level, increase our flexibility, stabilize our processes and make our production safer.” Cédric Vandevoir, Process Engineering Manager at SKF Aeroengine France: “The FMS has become an essential part of our production and contributes to our competitiveness and our success.”
“With the RoboFMS we can produce even the most sophisticated bearing components in the required quantities and the highest quality, and can thus supply our customers with customized rolling bearings within the agreed deadlines. The automation system makes a key contribution to this. The FMS has become an essential part of our production and therefore our competitiveness and our success. “
Gilles Ofcard, Factory Manager at SKF Aeroengine France, adds:
“With this automation project, we are ideally prepared for major changes in our industry. That’s because our sector is characterized by an increasing variety of products with ever smaller production batches. Naturally, some of us have reservations about such changes, which are due to the very high level of technical skills and the requirements for quality and performance in a competitive market. But we cannot resist this fundamental change, which is all the more reason for us to show that the technology helps us to further improve our quality level, to increase our flexibility, to stabilize our processes and to make our production safer.”
Marcus Jakob agrees with these statements:
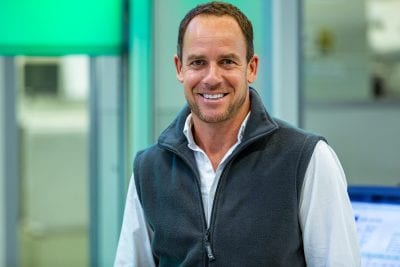
Marcus Jakob, Global Process Development Manager at SKF Aerospace: “Industry 4.0 digitalization and integration and automation of process steps are key priorities, so that employees can focus on quality and expertise.”
“With this project, we are blazing a trail at several locations within the SKF Group. We have already installed a second, identical RoboFMS at SKF Aeroengine in New York, supplementing it with an additional turning and grinding center.
A similar system is used at our Pennsylvania plant, where we manufacture special seals for the aerospace industry. Although it exclusively uses pallet clamping, which means that the system is less complex, the cooperation with our automation partner Fastems is paying off here too.”