When Mr. Liang Guihua, Chairman of Cepai Group Co. Ltd., made the decision to build a high-end automation system in 2019 for manufacturing small – down to 10 unit – batches of valve components weighing up to 1,000 kgs, he faced opposition or questioning from almost all senior executives and peers. “How would automation work for low volumes? How can we run various types of valves with different specifications, sizes, and materials – in a single system? How can we achieve quality with this method?”
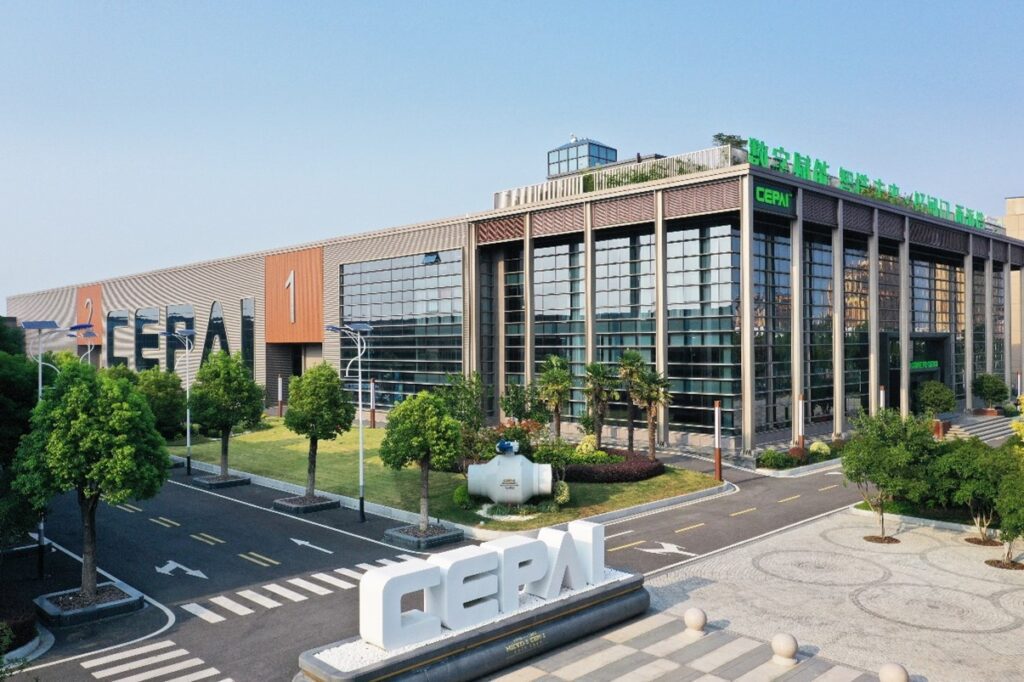
Today, the flexible manufacturing system (FMS) of Cepai integrates six high-end machining centers, is nearly 100 meters long, and has been successfully operated for over three years. It is probably the largest high-mix-low-volume automation system in the Asia-Pacific region, and it has already doubled the machine tool spindle utilization and increased the output per person hour by 60 %. The outstanding manufacturing performance has shattered all the doubts, and the FMS is today backbone of Cepai’s Intelligent Dream Factory, laying a solid foundation for the company to become a leading high-end valve manufacturer in China.
“For a manufacturer like us to excel, we must have unique advantages. For us in Cepai, it is the intelligence and flexibility“, Liang Guihua says.
In one year, Cepai has already doubled machine tool spindle utilization and increased the output per work hour by 60 %.
The Largest FMS in Asia-Pacific Region for High Mix Production
Founded in 2009, Cepai is a high-end manufacturer specializing in fluid control and specialized equipment for oil drilling, pipeline valves, control valves, as well as instruments. With their high-performance and high-precision products, Cepai has won business from the oil fields of PetroChina, Sinopec, Kuwait National Oil Company (KOC), Abu Dhabi National Oil Company (ADNOC), SONATRACH, and other leading energy companies.
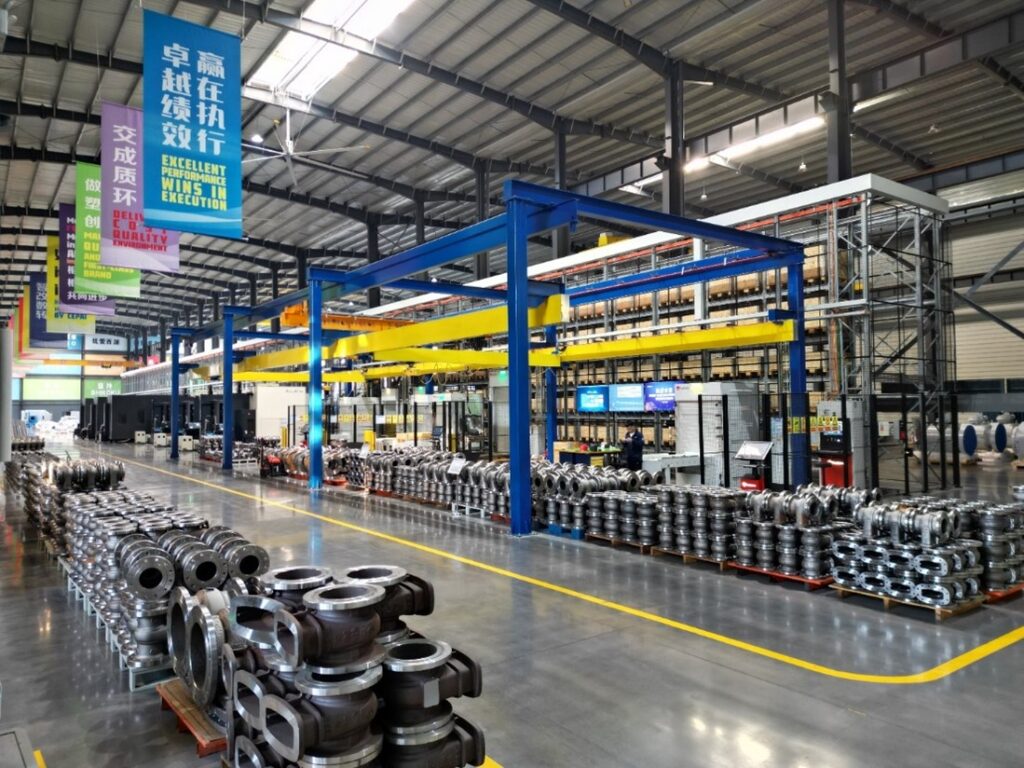
“The competition is – and will become – more intense with the domestic giants and overseas brands competing in all markets. In addition, the user demand is constantly changing, and we wanted to be competitive in being able to answer these needs fast and with top quality. A few years ago, we started planning on how to develop our manufacturing to more flexible direction, until we met Fastems in 2019,” Liang Guihua introduced. “Through the numerous success cases of Fastems in our industry all over the world, their FMS did what I had envisioned. Through multiple in-depth discussions, I truly understood what makes the difference between Fastems and traditional automation companies. Fastems always approached the topic from our individual manufacturing perspective and won my trust.”
Cepai’s FMS sets records not only in length, but also in the highest production mix and complexity in the industry. Cepai’s FMS integrates six 4-axis machining centers from Okuma and Makino, with different specifications and models. This does not only require the automation integrator to have a strong brand compatibility, but also a rich application experience. There are 159 machine pallets in the system of two sizes: 630×630 mm and 800×800 mm. In addition, there are 118 wooden material pallets of 1200×800 mm.
Robert Ding, General Manager of Fastems Automation Shanghai Co., Ltd., tells that integrating different machine tool brands, different pallet sizes, and material pallet management is not ‘off-the-shelf’ business for any automation company. The confidence that Fastems can undertake this project and ensure smooth operation comes from more than 40 years of experience in automating CNCs. The answers to questions such as which brand of machine tool is equipped with which interfaces, how to switch and recognize pallets of different sizes, and how the automation system can meet the changing user needs, have been addressed countless times in thousands of cases worldwide.
Moreover, the installation and commissioning work of the Cepai FMS was completed locally by our Chinese service team which has gained high recognition from customers. This is a strong proof of Fastems China’s positioning as a ‘global technical standard at local response speed’.
FMS Helped to Take Leaps in Processing Quality and Efficiency
When entering the workshop, the giant FMS stands right in front of us. The nearly 100 meters long and eight meters high pallet storage is neatly arranged. The stacker crane moves inside the storage, efficiently and orderly transporting various types of machining and raw material between six machine tools and three loading stations. The speed of the crane is 210 meters per minute and the whole system can be operated by two employees that are using the MMS control panel and clamping the parts.
“When Mr. Liang first asked me to be responsible of the FMS project, I was skeptical and even directly pointed out that our products were not suitable for automation,” recalls Chen Hui, Equipment Department Manager and Technical Leader of FMS at Cepai Group. “In my initial understanding, automation lines were meant for high volume manufacturing because switching from one job to another required large-scale adjustments to the production line, which would be slow and cumbersome. Our maximum batch size in valve parts is only a few hundreds, and we have a huge amount of different variants and specifications. Our production also requires extremely high fixture accuracy. How to automate such a mixed and high-precision manufacturing? It wasn’t clear to me until I saw examples on how Fastems systems are used – then I truly understand the difference between conventional automation and flexible automation.”
The weight of the parts ranges from a few to thousands of kilograms, with a minimum batch size of only 18 pieces. Both processing quality and production efficiency are in excellent level.
Fastems automation systems are controlled by the industry-leading Manufacturing Management Software (MMS) that is designed specifically for high-mix-low-volume manufacturing. It can simultaneously produce different orders, feed work to be processed in the machining centers, and switch between different parts fast and precisely. Fastems FMS is pallet-based, meaning that parts, fixtures, and pallets move as ready-built entities, achieving fast switching and processing of various jobs. Any part can be run with any machine, and the work is dynamically scheduled for the maximum equipment utilization and just-in-time deliveries.
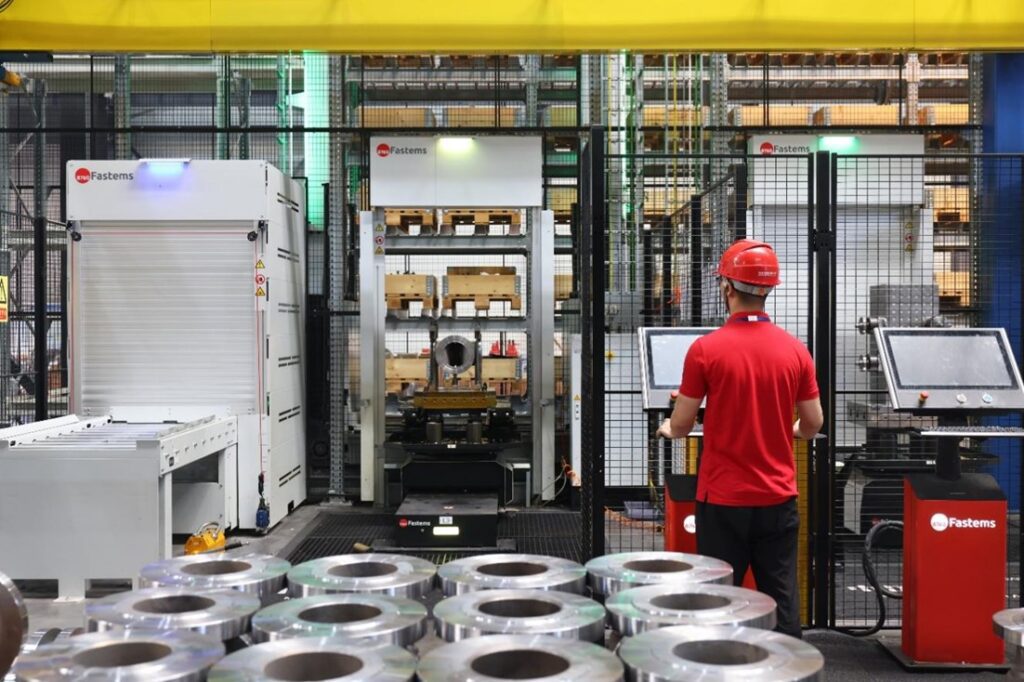
What is the current operating situation of the FMS? Chen Hui proudly shares: “Our manufacturing system has been running for about a year since its completion in the end of 2022. Multiple parts of various valves, including valve covers, valve bodies, pipe heads, and other components, have been added into the system. The weight of the parts ranges from a few to thousands of kilograms, with a minimum batch size of only 18 pieces. Both processing quality and production efficiency are in excellent level. For example, in our traditional workshop, a single machine would produce 7 parts in an 8-hour shift, whereas a single machine in our FMS produces 13 parts – almost doubling the efficiency. And another example, for ball valve body parts, the output from FMS is 32 pieces per machine, while a stand-alone machine in a traditional workshop could process only 20 pieces during a shift.”
The FMS also reduces heavy and repetitive manual work around the machining. Thanks to the automation control MMS, once a part has been introduced, it can be re-run any time in the future with just one click, instead to performing the lengthy setup work and test runs all over again. MMS informs operators in advance of all the resource preparations to be done, to ensure continuous production without machines needing to stop and wait for resources.
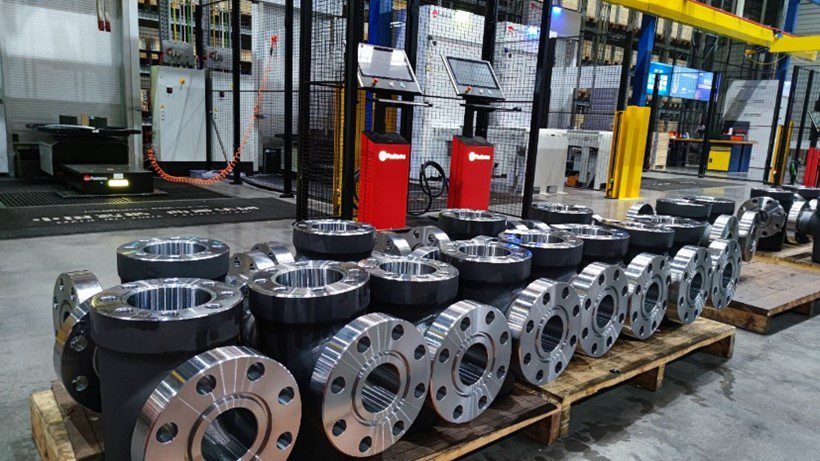
Expanding the FMS Way of Working
“80% of Cepai’s business is export to overseas, and our customers have very strict requirements on delivery time and product quality. Therefore, the stability and efficiency are what I value the most in our FMS. Fastems has lived up to our expectations. While effectively improving the processing efficiency, there have been a few system alarms which Fastems’ technical team have immediately responded and solved with an amazing quality.” Liang Guihua says. “In addition, the FMS has greatly enhanced our brand influence, receiving attention from the government, series of awards and honors, and the acquisition of resources. When our customers come to the factory and see our manufacturing system, they have greater trust in Cepai’s supply capacity and product quality.”
In the future, Cepai is looking for automating more of their operations and expanding manufacturing to other countries. “FMS is both a turning point and a starting point for Cepai. We plan to replicate our flexible manufacturing system in our traditional manufacturing sites after one or two years when we have finetuned the process and our team is more experienced with the technology. Additionally, we are investigating our expanding options to manufacture overseas, and the FMS method is something we can easily replicate without worrying about personnel and process issues,” Liang Guihua concluded. “With the continuous development of energy equipment industry, and more individual needs of customers, I firmly believe that flexible and digital manufacturing will become a major trend. We look forward to continuing to work together with the globally leading technology partners such as Fastems, and promote the development of high quality energy equipment manufacturing.”
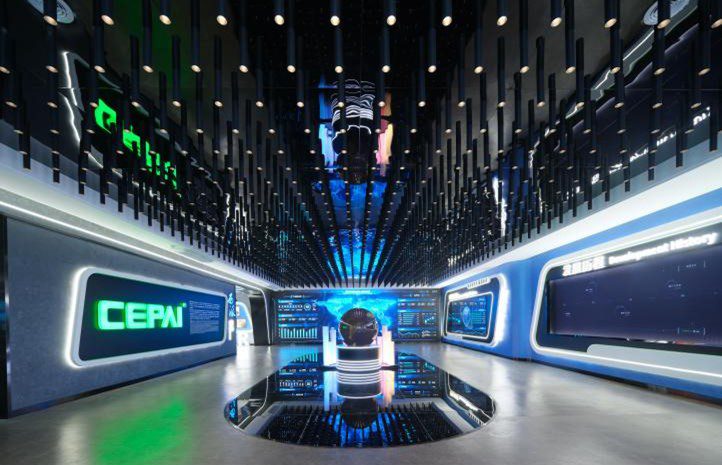