Kvalitetslego from Hälsingland
– From 6 to 18 pallets in a smaller footprint with Flexible Pallet Tower
THIS TEXT IS ORIGINALLY PUBLISHED IN AKTUELL PRODUCTION 06 | 2023 IN SWEDISH.
The locality of Alfta in Hälsningland in Sweden has long been a cradle for entrepreneurship and technology. What started as a village smithy in 1913 eventually became the forestry equipment company ÖSA, which reigned in the area for decades. Today, the historical ÖSA industrial area is home for around 25 companies. One of those companies is Alfta Kvalitetslego, a modern contract manufacturer with 60 employees and 30 Okuma machine tools, providing high quality and flexible machining for their customers in various industries. An important part of Alfta Kvalitetslego’s growth story lies in its values of customer satisfaction and a “zero-error spirit”, which have been aided by the company’s investment in automation.
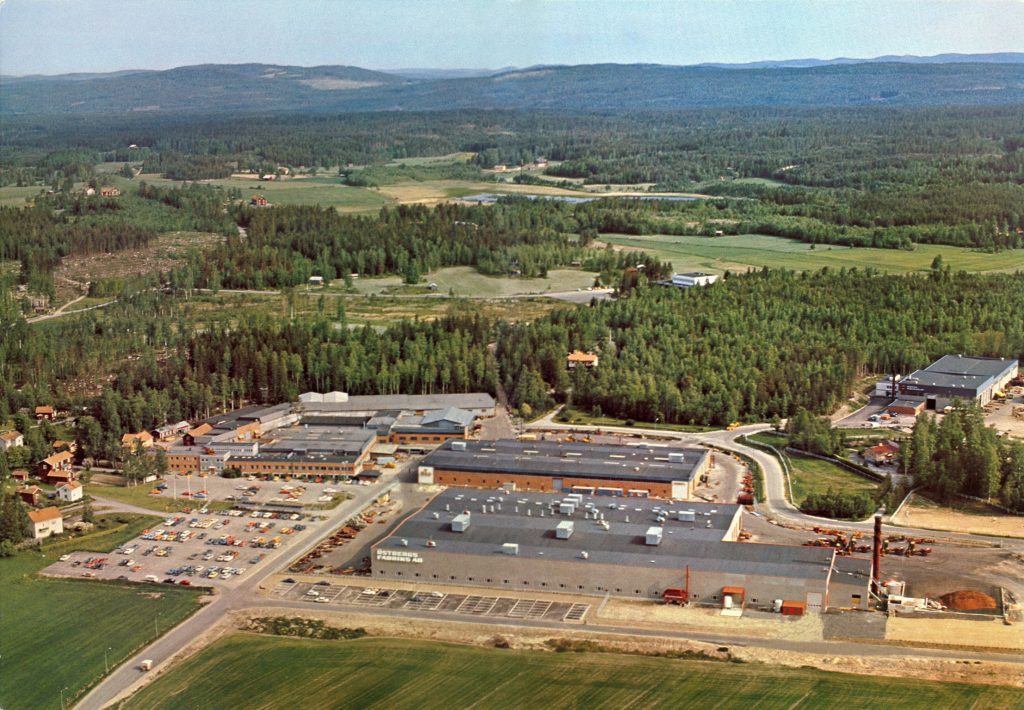
The historical ÖSA industrial area in Alfta, a hub for for forestry equipment manufacturing between 1952 and 1993, now housing around 25 companies with close to 400 employees.
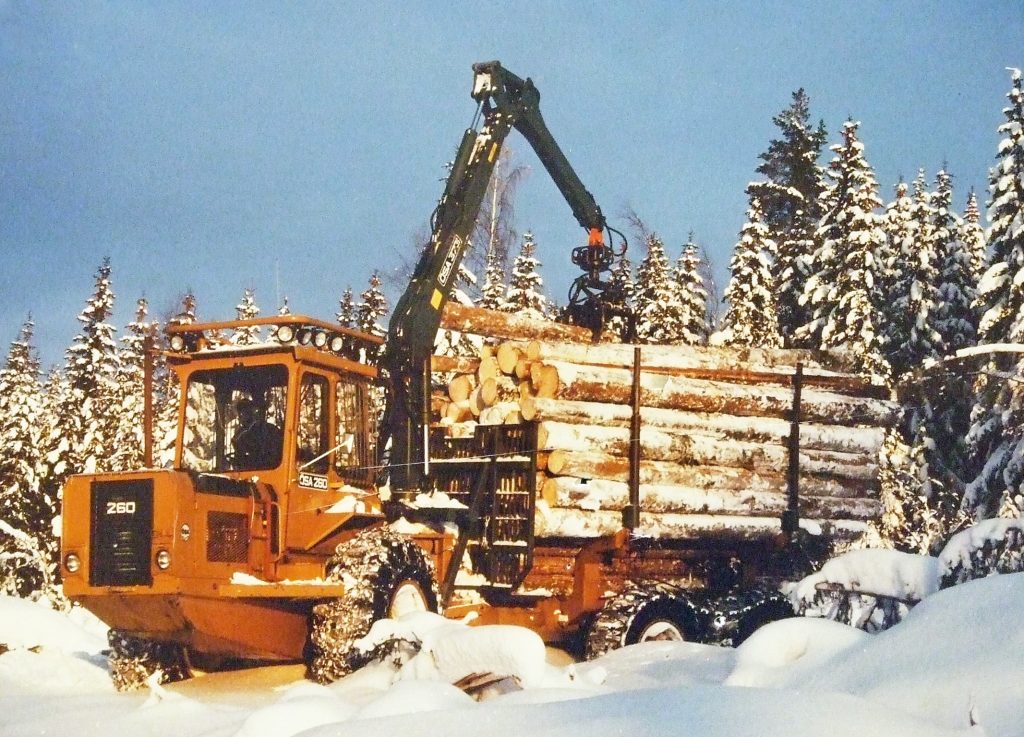
A bestseller from the ÖSA epoch – an ÖSA 260. 855 of these were made between 1976 and 1988.
Alfta Kvalitetslego AB was founded in 1991 by Åke Näslund, Hans-Olov Berg, and Stellan Hugg, all three experienced in mechanical production and construction. “We are a contract manufacturer primarily for parts that require high competence when it comes to precision machining in CNC lathes and multi-operation machines, with complementary circular welding,” describes Niklas Näslund, the CEO. Over the years Alfta Kvalitetslego has steadily grown along with its customers, for example with Komatsu and Engcon. The company has grown from 9 to 65 employees, with an annual turnover around 145 million Swedish crowns (around €14M) today.
Alfta Kvalitetslego pays homage to the Alfta locality’s roots in forestry equipment on their website, saying “Alfta Kvalitetslego is located in Alfta, in Ovanåker municipality, which has for decades served as the cradle for entrepreneurship both within the timber and forestry equipment industries. We like to underline that as a business, we have been heavily influenced by our surroundings of breathtaking nature and a strong entrepreneurial foundation.”
CEO Niklas Näslund says,” One reason why the company has been able to develop so positively is because we have strong customer focus, and a ”zero-error spirit”, which has allowed us grow alongside our customers. We have also always had the option to expand into already existing premises. What started in 200 square meters is now in 4,500 square meters, all under the same roof, without needing to relocate.”
Since 2019, Alfta Kvalitetslego has been owned by Storskogen, and now is part of their Industry business area, together with 25 other companies. ”Being a part of Storskogen means that we’re better positioned to further develop our company towards 200 MSEK (million Swedish crowns), and also allows us to have a really good exchange with our sister companies”, says Niklas.
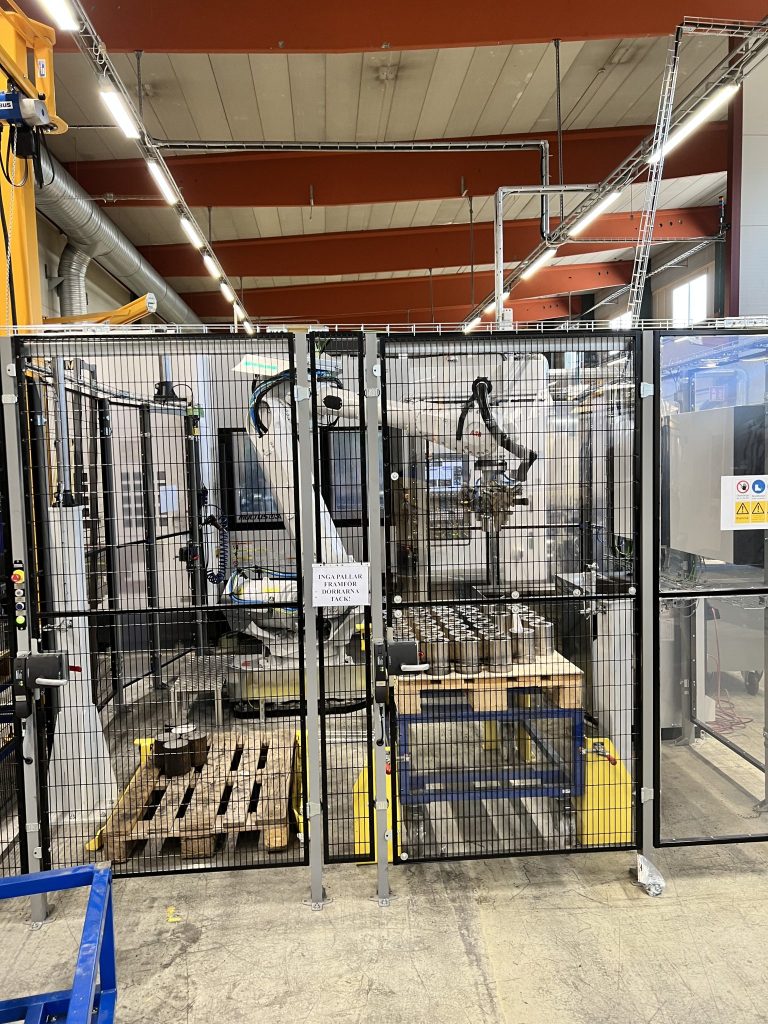
Robot cell loads and unloads workpieces directly from the pallet. Operators work in two shifts, and thanks to CNC automation, over half of the machine tools run unattended overnight.
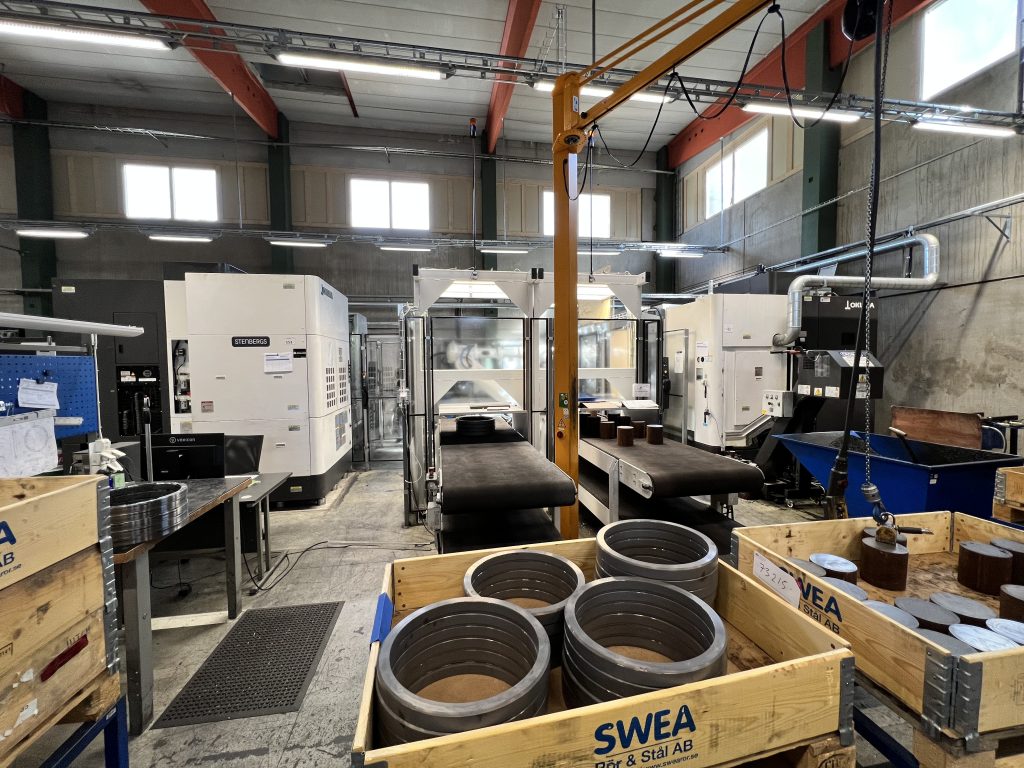
Robot cell feeding 2 machines, handling both raw material bricks and rings.
100% Okuma workshop
Today, Alfta Kvalitetslego is a company with cutting-edge production technology, including 30 Okuma CNC machines purchased from Swedish machine dealer Stenbergs.
”I mean, it is pretty unique”, says Niklas, ”That we’ve only bought Okuma machines to our workshop. The explanation for that is simply that Stenbergs has been doing a great job here with us for all these years. From the very start it was actually Stenbergs’ sales people that helped us find new customers, and that is really something we won’t forget. That is really what a partnership is.”
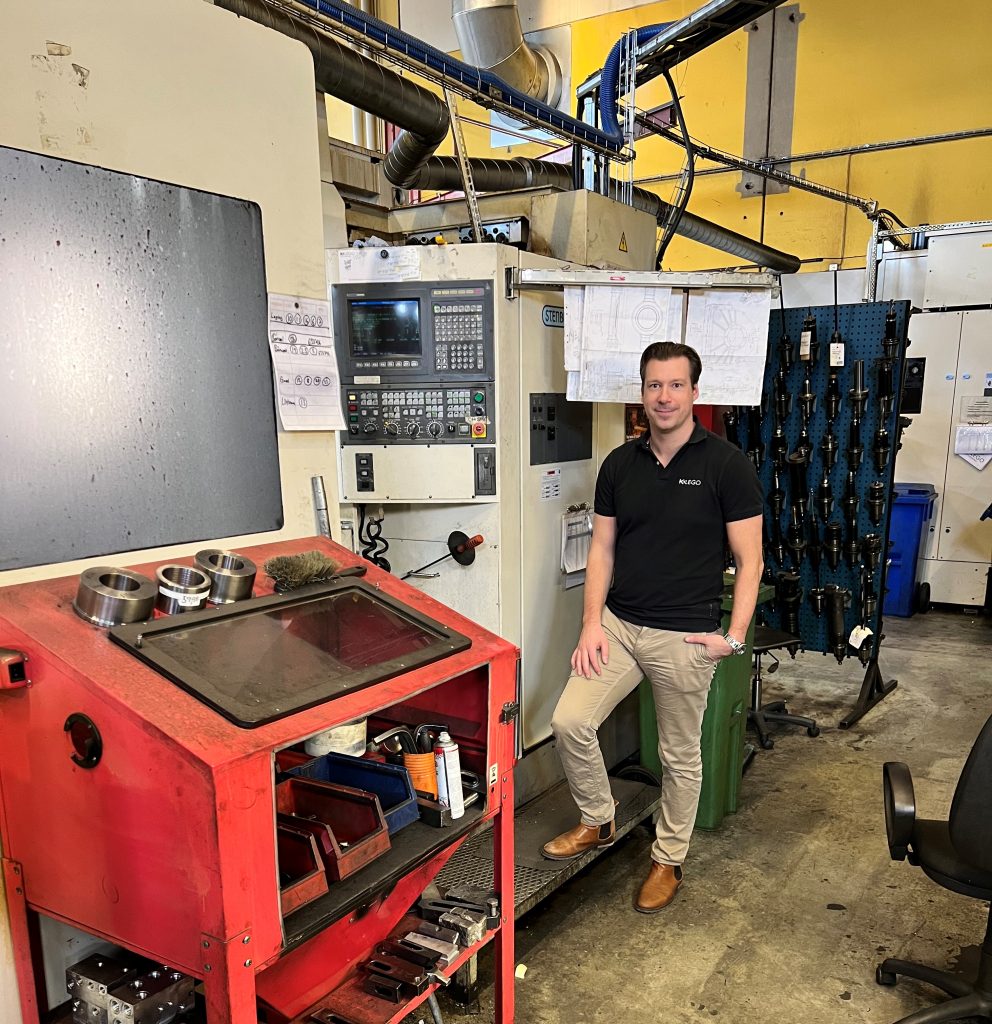
Niklas Näslund, CEO at Alfta Kvalitetslego, standing by the first Okuma that came to the company in 1994. Since then they’ve gotten another 29 machines from Stenbergs/Okuma, and the workshop is ”100% Okuma”.
Sweden’s first Flexible Pallet Tower from Fastems
Smart and effective solutions for maximizing the utilization rate of the machines is what is in focus for both Okuma and Fastems. As a result, the companies have had a very collaborative relationship which has resulted in – among over 500 other joint automation projects – Fastems’ Flexible Pallet Tower FPT, an extremely compact and efficient automation solution for 4 and 5 axis machine tools with and without automatic pallet changers.
Fastems, with 40 years of experience in flexible CNC automation and over 4,500 installations under its belt, launched the FPT at the end of 2021. The very first installation of which was at Alfta Kvalitetslego. FPT can accommodate up to 24 pallets from 300 mm to 630 mm, and it can be integrated with over 90 different machine brands, with a wide library of ready-made machine interfaces.
FPT offers the market a dramatic increase in machine tool utilization rates, and enables unmanned production. The plug-and-play automation system also decreases idle times and allows for economical production of high part mix, no matter what sizes the batches are.
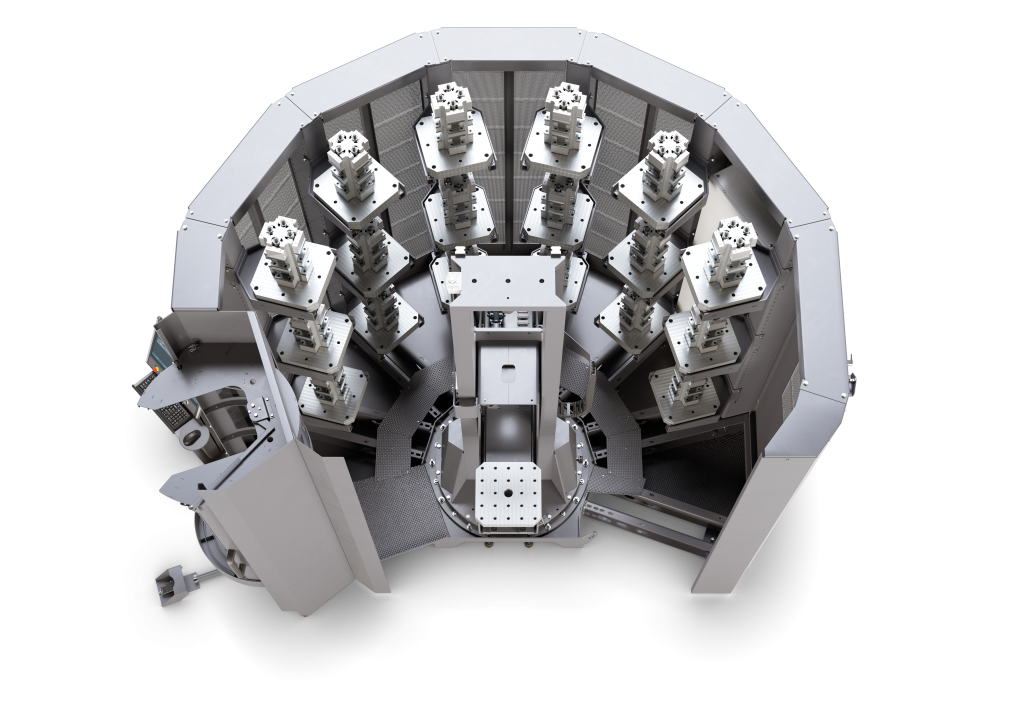
Compared to other similar systems for the market, Fastems FPT is compatible with over 90 machine brands, and machines both with and without automatic pallet changers. In addition to that, the solution is extremely compact: FPT-500 for 300-500 mm pallets only needs 9 square meters of space, and FPT-1000 for 500-630 mm pallets only needs 16 square meters. Instead of fixed storage capacity, like most of the other pallet towers, the FPT storage can be configured for up to 24 pallets in two to four levels, depending on load heights.
From 6 to 18 pallets in a smaller footprint
Alfta Kvalitetslego has had pallet systems since the early 90’s. With that extensive experience and knowledge, they quickly became interested in the new FPT from Fastems. Carl-Axel Karlström, Production Technician at Alfta Kvalitetslego says “Fastems’ new FPT is an extremely space efficient solution where we can fit 18 pallets in 3 x 3 meters, and with the accompanying Manufacturing Management Software MMS we’re able to keep the machine fed efficiently.”
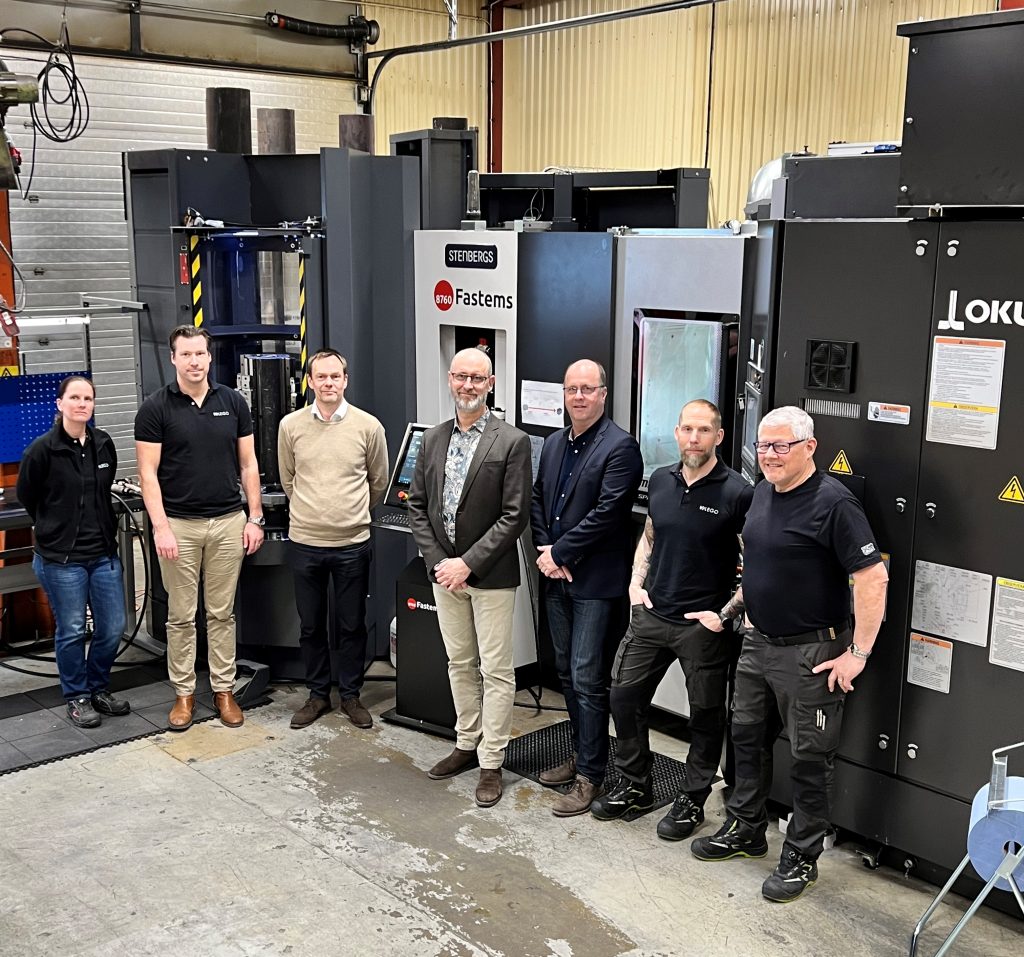
Sweden’s first installation of FPT at Alfta Kvalitetslego. Ramp-up of the system was underway in April when this report was made. From the left; Elisabeth Bäcklund: Technical Director, Niklas Näslund: CEO at Alfta Kvalitetslego, Henrik Broden: Sales Manager for Scandinavia at Fastems, Gunnar Strömmer: Regional Sales Manager in Norrland, Pierre Huss: Sales Manager at Stenbergs, and Carl-Axel Karlström and Fredrik Brandt: Production Technicians at Alfta Kvalitetslego.
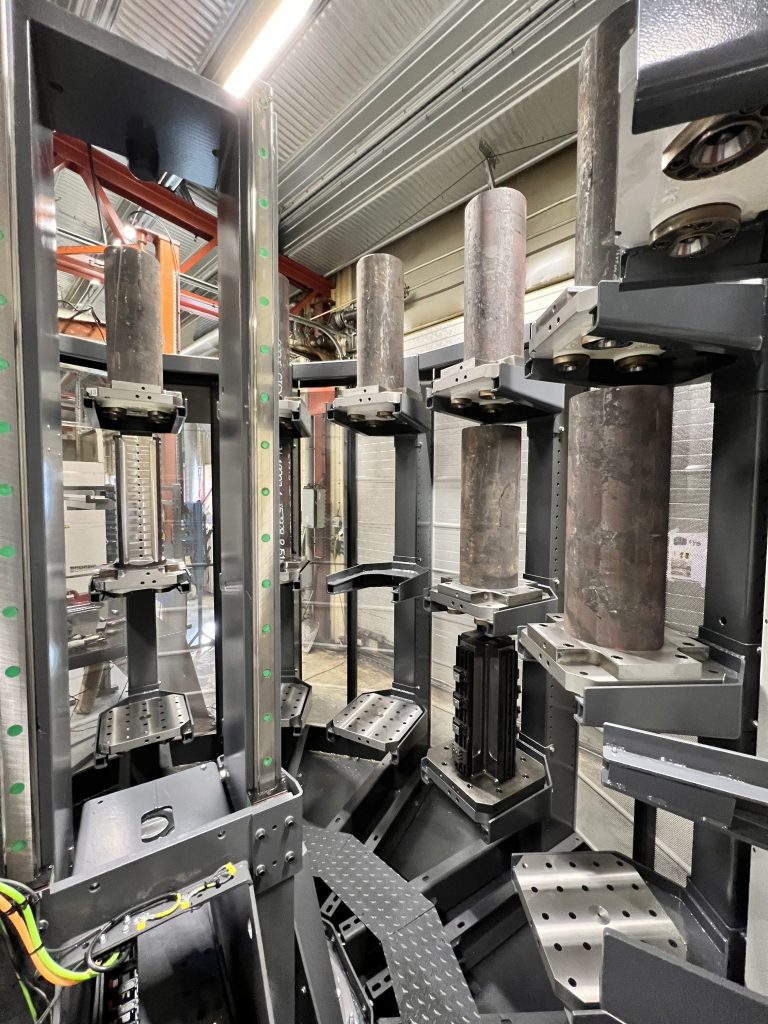
The new FPT from the inside – 18 pallet places built vertically in three levels make for an extremely space efficient automation solution.
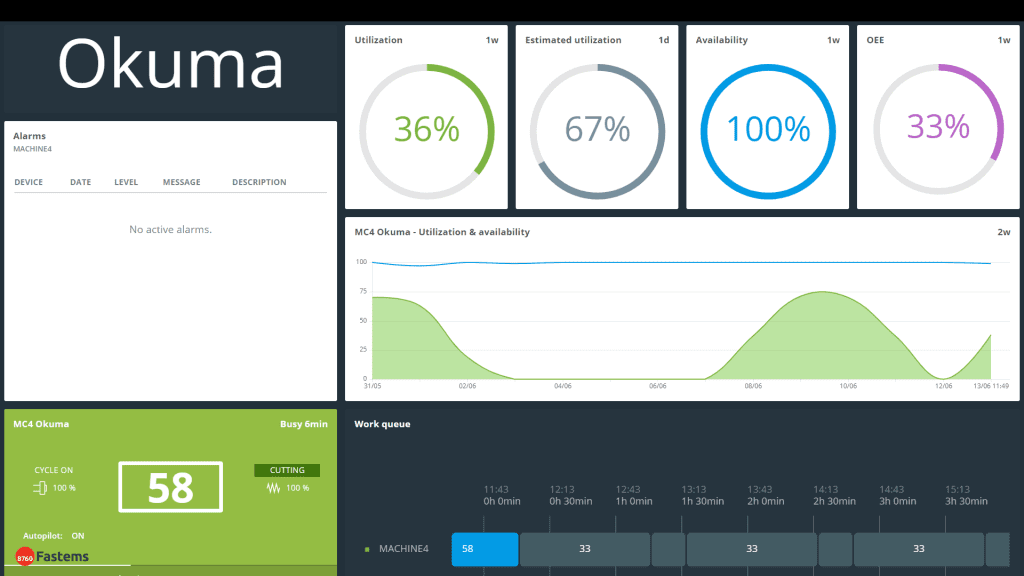
Manufacturing Management Software (MMS) by Fastems is the production control software for FPT. The features include easy single screen user interface with drag-and-drop production orders, bringing new work pieces into production in under 60 seconds as well as automatic production order generation based on intervals or inventory levels.
THIS TEXT IS ORIGINALLY PUBLISHED IN AKTUELL PRODUCTION 06 | 2023 IN SWEDISH. LINK TO THE ORIGINAL ARTICLE HERE.