The Fastems’ Work Cell Operations (WCO) combines production and resource planning of stand-alone machine tools and other manually operated workstations under one control. WCO’s functionality and value can be greatly extended with the right kind of production machinery interfaces. Usually, at this point stuff tends to get quite technical and the discussion can easily lead to concepts such as DNC, MTConnect, I/O and Focas, just to name a few.
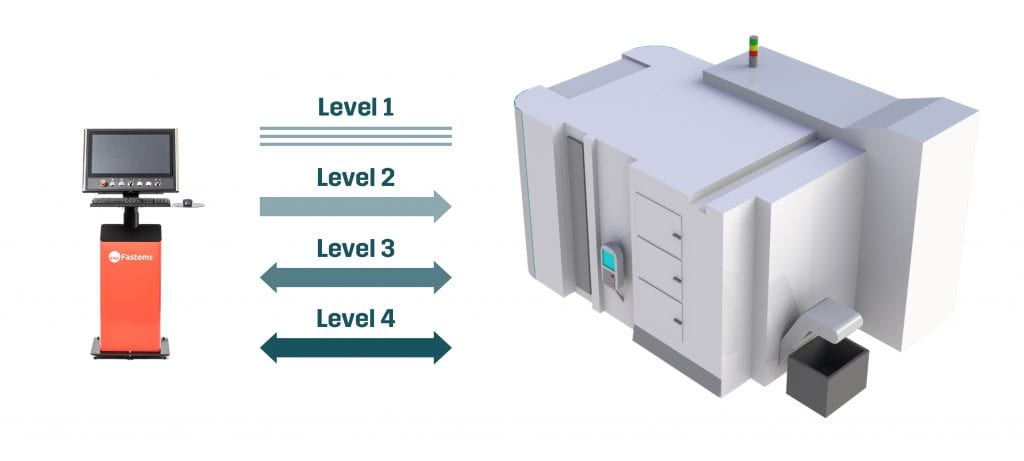
The four distinctive levels of Fastems’ Work Cell Operations.
Usually, a good starting point for simplifying this discussion is to group the different interface types based on their functionalities and the value they bring to the production. The idea is, that each WCO connected machine or workstation can be equipped with the right kind of interface according to the use case. We at Fastems like to describe the different interfacing possibilities through four distinctive levels. Naturally, one WCO installation can have machinery with different interfacing levels.
Level 1 – No device interface
With the first interface level, there is no interface to the machine tool so there is no real data transferred between the WCO software and the machine tool. However, the operator still gets clear and prioritized work lists from the WCO which are automatically formulated by the MMS based on the real production orders and their due dates that have been input to the system. This helps operators plan their daily work and to know what jobs are the most critical ones at each point. The worklist is of course automatically updated if production orders change. Level 1 functionality, just as on other interfacing levels also, can be extended with production documents, which makes all the needed work documents and instructions automatically available for the operator whenever needed.
✔️ Up to date worklists for operators (included)
🔘 Production documents and instructions (optional)
✖️ KPI monitoring (not included)
✖️ NC program transfer (not included)
✖️ Tool Check (not included)
✖️ Tool data transfer (not included)
Typical applications: different manual work phases such as manual machine tools, saws, manual deburring, and inspections.
Interface Level 2 – Status monitoring
On the second interface level, a basic level interface is built between the WCO and machine tool to get the status signals from the machine tool. These updates can then be used in real time status monitoring as well as to calculate Key Performance Indicator (KPI) values for the machine. The Level 2 interface can be implemented for example by using MTConnect or a separate simple connectivity box that receives the status signals from the machine tool wiring.
✔️ Up to date worklists for operators (included)
🔘 Production documents and instructions (optional)
✔️ KPI monitoring (included)
✖️ NC program transfer (not included)
✖️ Tool Check (not included)
✖️ Tool data transfer (not included)
Typical applications: older standalone machine tools without DNC, and production devices where the status signals can be received from the wiring.
Level 3 – NC program transfer and tool check
On the third interface level, there is already two-way data transfer to the machine tool. The NC programs can be transferred between WCO and the machine tool in both directions. This makes NC program management easier, because the operator can always be sure that the latest version of the NC program has been downloaded to the machine controller. On top of this, the user is able to see the tool magazine content from the WCO screen. MMS automatically calculates the needed tool resources for each job and informs operator about the missing tool resources. This makes the operator’s work easier and more efficient because it is clear which tools must be added to the magazine to run each job.
✔️ Up to date worklists for operators (included)
🔘 Production documents and instructions (optional)
✔️ KPI monitoring (included)
✔️ NC program transfer (included)
✔️ Tool Check (included)
✖️ Tool data transfer (not included)
Typical applications: standalone machine tools with DNC capabilities.
Level 4 – Tool data transfer to the machine tool
This is the ultimate level when it comes to combining the WCO and machine tool together. In addition to the capabilities of levels 1-3, the fourth level also enables eliminating human errors from the tool offset handling. This is because the tool data is automatically transferred to the machine tool when the tool is inserted to the magazine. This combined with the presetter interface makes daily tool management as easy as possible. The functionality can also be extended with tool ID chips if needed.
✔️ Up to date worklists for operators (included)
🔘 Production documents and instructions (optional)
✔️ KPI monitoring (included)
✔️ NC program transfer (included)
✔️ Tool Check (included)
✔️ Tool data transfer (included)
Typical applications: standalone machine tools with DNC capabilities.
As previously mentioned, the WCO can combine many different stand-alone machine tools and other manually operated workstations under one control, creating an enormous benefit by having a clear view of the big picture. When delved deeper into the topic, the benefits and outcomes of each machine tool and workstation come from the interface levels that need to be evaluated together. Luckily, we have extremely skilled professionals to help piece together the review and study, so there is no need to get intimidated by the technical descriptions. Hopefully this helped you to get a first level understanding about machine interface level opportunities. Do not hesitate to contact your local Fastems sales representative to discuss more about WCO and all the different machine interfacing possibilities.