This article written by Tord Käck was originally published in the latest issue of Aktuell Produktion’s digital newspaper.
The manufacturing industry is evolving alongside the world economy’s quickly changing needs and trends. The industry is facing many new challenges, and at the same time opportunities, which force manufacturing companies to stay alert in rethinking how to build and construct the base of their businesses. In the world of metal cutting industries, the biggest identified challenges now are the increasing complexity and variety of products, as well as shortening of product life cycles, delivery times and planning horizons. In addition, rapid shifts in technology and business, rising demands for quality, increasing traceability requirements, and pressure to reduce capital tied up in inventory, season the mix causing extra push. On top of everything, when you try to solve one challenge, you might face a new one. A holistic and flexible solution is needed to face current and future challenges, and to take automation beyond machine tending.
With experience of over 35 years, we’re aware of the ever-changing challenges in the manufacturing industry. This is why Fastems offers flexible automation solutions all over the globe, helping manufacturing companies in the metal cutting industry to overcome the various challenges the industry is facing. One of the core enablers of our flexible automation solutions is the Fastems Manufacturing Management Software (MMS),which has been an inseparable part of our automation offering for over 20 years.
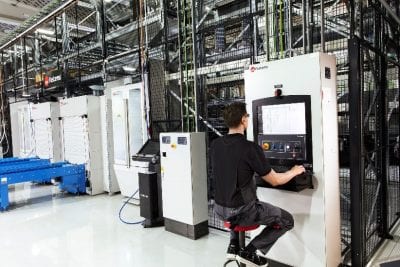
Fastems’ flexible automation solutions come with intelligent Manufacturing Management Software (MMS). MMS can be used easily from the office and from the factory floor.
MMS is part of the winning recipe for how to over come the challenges mentioned above. It helps tackle complexity and increasing demands by scheduling production, calculating resource needs, and communicating the right information to the right people. Much like an orchestrator for the entire automation system. Thanks to MMS, tools can run 24/7, day and night – 8760 hours a year. Now, MMS also provides machine interfaces that enable the integration of automated and non-automated manufacturing, which is unique in the metal cutting industries. It takes automation beyond machine tending.
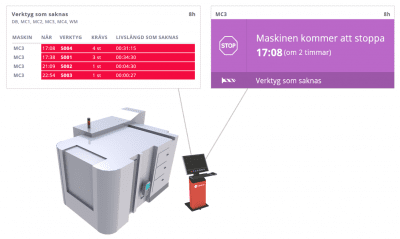
Fastems MMS provides all the information needed to keep machine tools running 24/7. MMS’s predictive tool check provides information about the upcoming tool shortages even days ahead.
While MMS has been available for Fastems’ automation customers for quite some time, we are now able to provide similar capabilities for stand-alone machines and other non-automated operations as well. We call this feature Work Cell Operations (WCO), which is one part of the MMS. WCO brings the well-recognized scheduling benefits of FMS to stand-alone machines. Manufacturers can connect all stand-alone machines under one control, effortlessly taking care of scheduling and handling resources. In addition, many advanced interfaces are available to WCO connected machines enabling status monitoring, NC-program transfer and tool offset writing to the machine controllers.
In order to bring the functionalities of WCO to a factory, one doesn’t need to have existing Fastems automation. WCO can be brought to your factory floor to integrate stand-alone machine tools and other manually operated workstations into one system. In turn, this will allow you to monitor and manage the schedules, worklists, NC programs, tool data, and decrease the amount of manual work. On the other hand, existing Fastems automation solutions can be extended with WCO.
Making daily production planning easier in a machine shop
Two years ago, a subcontracting machine shop invested in a Fastems pallet FMS (Flexible Manufacturing System) with two integrated horizontal milling centers. Orders are imported automatically through the ERP-interface to the Fastems’ MMS software, after which the MMS automatically allocates the machining jobs to the HMCs. The MMS also takes into account the needed tools and materials and informs operators about shortages several hours before they start blocking production. The company started noticing the full benefits of MMS in only a couple of months after the project delivery: practically no human intervention is needed after a new order is inserted to the ERP of the customer. The investment has resulted in increased utilization of the machine tools as well as improved delivery accuracy since the fine scheduling is based on real production orders and their expected delivery dates.
The company was impressed with the results, which encouraged them to extend the MMS fine scheduling to cover the stand-alone machines as well. Specifically, the customer decided to purchase the WCO extension for their existing Fastems system for 10 stand-alone machines. The stand-alone machines connected to WCO are mainly turning centers and some are also equipped with robotized machine tending cells. Integrating individual robotized machine tools with WCO is not an issue: MMS can calculate the work queue for the robotized machine, and can also check the status of the cutting tools – if the interface to the machine tool is available. Through this, the customer was able to utilize their existing factory computers as MMS workstations, making the commissioning and installation of the system a really quick process.
The extension was installed at the beginning of 2020 and the customer is eager to see the power of MMS fine scheduling throughout their entire factory. The initial experiences with the extension have been extremely encouraging and the production will be ramped up gradually once all the production master data, such as part routes, have been added to the system.
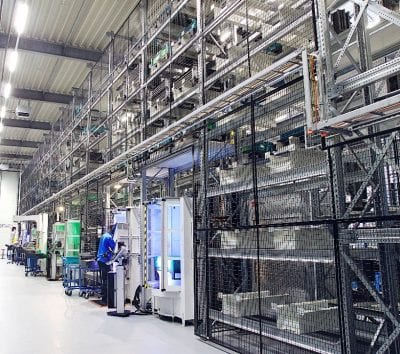
Fastems FMS solution can be extended with MMS fine scheduling to cover the stand-alone machines as well.
How does the Work Cell Operations of MMS work in practice?
Worrying about software related details isn’t an issue, because of how WCO is part of MMS. This means a manufacturer can operate with a single software regarding the production planning. In general, the basic concept of MMS is brilliantly simple: a production order is inserted to the system using either an intuitive web-based MMS user interface or through the optional ERP-interface. After receiving the order, MMS fine schedules the production order based on delivery date and required production capacity, and then automatically generates work lists for the shop floor operators. If new production orders are inserted, or the existing ones are modified, MMS automatically reschedules everything and generates new work lists. In the background, MMS also calculates needed production resources such as cutting tools, NC programs, work setups and raw materials, and compares them to the current resource situation. If for example a turning machine has the wrong setup active to run the next machining job, the operator is guided to change the setup before starting the job. It is also possible to attach work instructions, drawings and other production documents to each manufacturing step, making them easily available to the operators when needed.
MMS also takes care of the material flow between manufacturing operations: as soon as the parts have been marked as complete from the previous, a transfer task is automatically generated by MMS to take the parts to the next operation. This makes the logistics operator’s every day on the job quite a bit easier.
The outcome especially with MMS WCO is that the production planner knows what is happening in the production and when parts are finished, how the connected machines are running, and he can monitor the outputs with an ease. The production planner saves time and is be able to work on other things. For the operator it is easier to execute tasks because there is only one software telling exactly what needs to be done and when.
Naturally, the WCO of MMS works seamlessly together with Fastems’ pallet and direct part handling automation – the two other domains of MMS. This means that parts can first be machined, for example, in a fully automated Flexible Manufacturing System (FMS), then transferred to stand-alone machine tools and lastly to final inspection. All these operations can be taken into account in the automatic fine scheduling. It is also important to recognize that the WCO connected machines are not limited to machine tools: WCO can just as well generate a sawing list for a sawing cell operator or a work list for a manual deburring operator. The amount of different WCO application possibilities is huge. Thus, one could say that the MMS Work Cell Operations can be seen as a true connector between the automated and non-automated manufacturing operations.
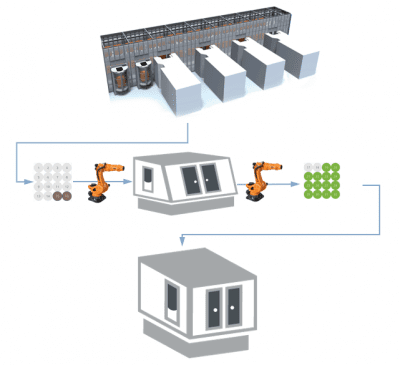
Three MMS domains, Pallet MMS, Part MMS and Work Cell Operations work together seamlessly, making production scheduling transparent even when a part goes through both automated and non-automated manufacturing steps.
Status quo – Excel and spreadsheets
Even today, production planning in many machine shops is still done with Excel and spreadsheets. Although this may work to some degree, ultimately this method requires a lot of manual planning work to keep the production plan up to date and to communicate the updated work lists to the factory floor operators as well. MMS helps streamline the process, meaning that the time of production planners can be used more productively. This means eliminating the need for manually updating the spreadsheets and running around the factory floor several times a day just to keep the production on a correct track. Now the stand-alone machine tools and other manually operated workstations can run smoothly in the same production process.
This article written by Tord Käck was originally published in the latest issue of Aktuell Produktion’s digital newspaper. To read the original text in Swedish see page 50 of issue No 3/4.