Development-mindset and flexible automation make a local machine shop pioneer
Joensuun CNC-Machining Oy has grown to be a local pioneer of metal shops in Finland. This development is based on significant investments in flexible, automated, and intelligently controlled manufacturing, thanks to which the company has multiplied the value of its multi-axis machining expertise for its customers and business. A key enabler of the development has been the Fastems’ Flexible Manufacturing System (FMS), together with the intelligent Manufacturing Management Software (MMS) for production planning and resource management.
Note: article available as shorter version in Finnish in Eurometalli magazine’s 7/2021 issue
Executive summary
- In 2018, Joensuu CNC machining first automated two 4-axis Mazak HMC’s with Fastems MLS system with great benefits in machine utilization, lead times, production planning, employee engagement, safety, and more. The system was extended with a third Mazak in 2021.
- As the next step in 2020, the production planning and operator guidance of the entire shop (excluding one saw) were were automated using Fastems’ Work Cell Operations software, which is part of the Manufacturing Management Software suite. As the result, the production in total is transparent and better optimized based on customer orders.
- Development mindset, brave investments in automation, and working methods development have made the company a pioneer of metal shops in Finland.
Putting Joensuu on the map
Established in 2007, Joensuun CNC-Machining is a contract supplier of high-precision machined sub components and sub assemblies located in the eastern part of Finland. The company serves customers in the forestry, mining and environmental technology sectors. Employing more than 30 people and running a turnover of approximately EUR 4 million, the machine shop aims to increase its market share by means of machining expertise and flexible customer service. CNC-Machining provides customers with a very wide range of components and, if necessary, fully completed, assembled products.

CEO Petri Holopainen and Quality and Development Manager Juuso Herranen with one of FMS’s workpieces.
Joensuun CNC-Machining mostly produces batches of 5–30 pieces that recur on a weekly or monthly basis. This makes the company a typical example of a subcontracting machine shop that produces small series of varying but recurring parts. The continuous flow of production includes almost 1,000 different items each year. In practice, this means a throughput of about eight million kilograms of metal. At the same time, almost 140 tons of chips are cut off. What is more important than the material throughput, however, is the added value the company produces for its customers, i.e. the machining and other services, which generate the majority of the turnover. Run by an entrepreneur in his thirties, the business generates an annual profit of approximately 20%. It is also worth noting that Joensuun CNC-Machining Oy has not had a single day of layoffs during the COVID-19 pandemic, and it is thanks to automation that the cost level has been kept under control even during quiet periods.
The operations of CNC-Machining combine visionary courage, the best technologies, and continuous improvements. The company acquired a flexible automation system from Fastems in 2018, as well as the Work Cell Operations (WCO) software for the production planning and resource management of the entire machine shop in 2019. What changes have these systems made for CNC-Machining Oy? Let’s first go back to the period before the FMS investment.
Straight to the “deep end” of automation
CNC-Machining started considering an automation investment for horizontal milling machines back in 2014, when the company’s management first got acquainted with a flexible automation system. The idea started to become reality in 2017, when the company made an investment almost equal to its turnover, which was around EUR 2.8 million. One part of that was the automation of two 4-axis Mazak HCN-6800 machine tools with a Fastems FMS (MLS-MD). Commissioned during 2018, the system took over about half of the company’s production at the time. Currently, about 300 items are constantly flowing through the FMS. Petri Holopainen, the CEO and largest owner of CNC-Machining, has been satisfied with the development investment from a few years ago and the impact it has created.
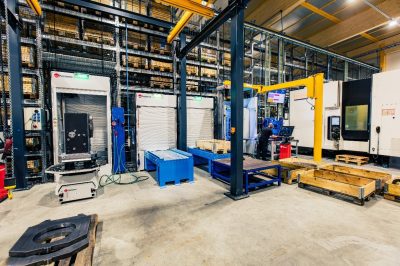
The picture shows the FMS deployed in 2018. On the left, there is a loading station for larger pieces, two material stations and a loading station for smaller pieces. On the right, there are two Mazak 4-axis milling machines.
“The system has paid for itself in less than three years. At the same time, the amount of overtime and sick leaves has decreased, and the staff is more committed and coping better. The working methods and ergonomics have also improved, and many workpieces that previously had low profitability have become much more profitable. We are also in a fortunate position when we made this sizeable investment well in advance of the overall development of the sector, so the investment has brought us a great market advantage. The machine utilization rates have been increasing all the time, and the size of the investment shows how strategically important it has been for our company,” Holopainen says.
Quality and Development Manager Juuso Herranen agrees with Holopainen.
“The FMS project threw us straight to the deep end of development, and we immediately experienced benefits of automation that we could not really predict when making that investment. With the automation, our operating methods have become more systematic and standardized. This has brought major benefits, especially when our non-automated machine tools were put under Fastems’ WCO production management software in the second phase of the investment. The system has also made production more effective and reliable: even if there are sometimes sick leaves, for example, one person would be enough to control the production of two machines in the system,” Herranen says.
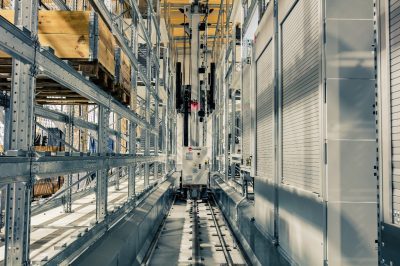
The FMS stacker crane serves machine tools with machine pallets, but also transports material pallets, enabling efficient space use and optimized material management.
We will get back to production control with the Work Cell Operations (WCO) software a bit later in this article. Right now, the two men are still looking back at the FMS investment a couple of years ago with apparent satisfaction. On the other hand, it is beneficial to learn from all experiences: what went well and what could have been done better or in a different way?
“Fortunately, we did not start by investing in a smaller automation system, because the storage of the material pallets would have required a much bigger building and many forklift drivers to run the logistics; our workpieces are quite large. Therefore, material management largely tipped the scales in favor of the Fastems solution, and we’ve been satisfied. At the time, the system was designed very thoroughly with Fastems, which for example, could be seen in numerous layout suggestions. In retrospect, however, there are two things that we could have done differently. Firstly, we could have invested a little earlier, and secondly, we could have paid even more attention to the extensibility of the system and preferably made it extensible to the old building. However, the funding was already tight enough, since the investment was very large,” Holopainen says.
Herranen confirms:
“Even stronger planning for the future with a ‘what happens when this is no longer enough’ scenario would have been necessary. At the time, we were focusing more on finding enough work to match with the capacity of the system.”
As a result, after three years, the company has just integrated a third Mazak to its MLS system, and has also considered extending the entire system. CNC-Machining’s experience exudes positivity and humanity: they were blown away by the benefits of automation, and the company has been making excellent profit. Fastems is familiar with such a situation, as almost 80% of the automation systems supplied are extended after 2–3 years of operation.
An intelligently controlled automation system ensures efficient production
The key features of Fastems flexible manufacturing systems are automated production planning and production resource management. This way, the systems enable high machine utilization rates combined with timely production. In practice, this means economically viable, flexible small-batch manufacturing.
Holopainen illustrates the situation with an example:
“Earlier, for instance, when working on an order of a certain product family, the machine was dedicated to that one order for about two weeks, thus we couldn’t take orders from other customers. The flexibility brought by FMS allows the Mazaks to always produce the necessary number of pieces, since the Fastems MMS handles the production planning and ensures the availability of the necessary resources in advance. Due to the long machining times of these particular workpieces, it has been specified in the FMS production plan that they are made at night during unmanned periods.”
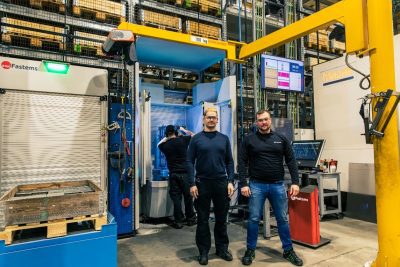
Herranen and Holopainen in front of the FMS system, with operator Paavo Pärnänen in the background. Raw material billets on the left and a configurable dashboard screen on the top right. The system is controlled using the red station commander.
Next, Holopainen opens the MMS control on the conference room screen to check the situation and discusses in more details the benefits of the lights-out manufacturing.
“Today, for example, the data indicates that the machine was running all night, and the first break did not come until nine o’clock in the morning. The machine utilization rates have been increasing all the time, and we are moving step by step towards 8,760 annual hours. At the moment, one limiting factor is the insufficient number of tools in the machine magazines, because we need many different tools for aluminum products. Here, the third Mazak with larger tool magazine helps.”
Some of the other FMS benefits arise from the development of work methods and fixturing solutions necessary for the introduction of automation. Herranen explains:
“For the FMS, dedicated machining towers were designed and a fixturing standard was created. The fixture change times and process are now completely standard, and the set-ups can be made in the loading station while the machines are working on other pallets. We manage the fixtures through the MMS fixture library. The same approach has later been adopted on the WCO-controlled machine side, so the fixture solutions used in the FMS can be borrowed for manual machines and vice versa, if necessary. We always make NC-programs in CAM and never using machine tools themselves. The NC-program library is under MMS control for the pieces produced in the FMS system.”
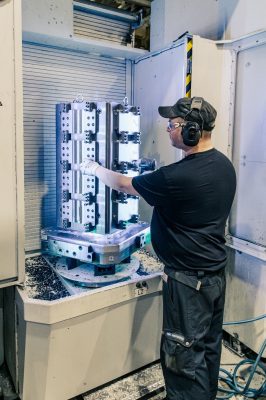
Operator Paavo Pärnänen is working at the FMS loading station. The working positions are ergonomic and the lighting is good.
So, automation requires some standardization and planning, but once they are done, efficiency increases significantly. When the Fastems MMS control manages the production resources, such as the fixtures, NC programs, and raw materials, and knows the “recipe” for producing the piece, it is able to ensure the realization of the planned production in advance, also in the world of varying small batch production. The role of the production manager then advances from mere firefighting to actually managing the production. The daily life of operators also dramatically changes for the better.
“There is a huge shortage of skilled workers in the industry, and one idea behind the automation investments has been that automation enables faster learning of the operator’s tasks. This year, we have recruited five new employees, two of whom did not have any previous machining experience. Nevertheless, these operators have been able to work independently in loading tasks after about one week of training. Our goal for the future is to develop cooperation with educational institutes, because we will certainly need more employees. Automation also polishes the employer’s image in the sector, because the work is now much cleaner and less burdening than its traditional reputation,” Holopainen says and then concludes:
“We care about our people, and automation paves the way for more meaningful, ergonomic, and safe work.”
To summarize, the benefits of the Fastems MLS automation include:
- The investment paid back in three years.
- The machine utilization rates have increased tremendously. At the same time, unit costs have decreased and pieces with low profitability have become profitable.
- Intelligent production control and resource management help to work proactively and keep production easy to manage.
- Work method standardization and fixture design enable efficient processes.
- The work of operators has become safer and more meaningful. Manpower is easier to find and training for work is smoother.
- Delivery times for customers are more reliable and the manager sleeps better at night when production can be relied on.
- The quality has increased and stabilized as physical operations are standardized and run by automation.
Work Cell Operations automates the entire production
Around 2019, the Joensuu people realized that the production of machines in the FMS system could be predicted and monitored in real time, but this was not possible for the company’s other machines or production cells because they had not been connected to the Fastems MMS control. At the 2019 EMO fair, Fastems introduced the Work Cell Operations MMS module package for the automation of manual machine tools, i.e. those outside a physical automation system. WCO manages the production resources, such as the raw materials, and creates an automatic production plan based on the orders, guiding the operators in its implementation. This makes the production transparent, efficient, and predictable to the accuracy of one minute – four full days ahead. The software can be deployed as such, without any automation hardware, or as part of a larger automation system, which is the case with Joensuu.
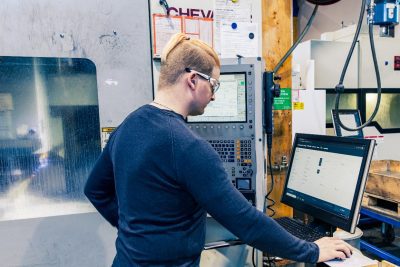
Herranen is presenting a WCO-controlled three-axis milling machine. In addition to the work list, the operator receives work instructions on the screen.
In Joensuu, the WCO features began to be deployed in spring 2020, and since then the company has been a pilot customer of Fastems. In practice, Fastems is developing the latest features of the software together with the company.
“After the sawing machine, our entire production is planned and driven through the WCO control. We can now see production peaks more clearly, and the system automatically prioritizes the most urgent orders, which naturally balances the production. Since the same MMS software is running in the FMS system, the overall situation and the related data and analytics are all managed in one place. The next step is to think about how we can make better use of the data. Data like this is also accurate enough for the continuous development of operations, meaning that we don’t just look at the bottom line every now and then to check that we are doing alright,” Herranen says.
“WCO together with our ERP system make an excellent package. When the material arrives in the ERP, the control will see what material is available, and the most urgent order will get underway. Previously, the production manager had to monitor the arriving materials and assign orders to each machine manually,” Herranen continues.
For the operator, WCO means a clear and prioritized work list to focus on. The software also enables paperless production, as each production item can be combined with documents, such as work instructions or drawings, in the MMS system.
Joensuun CNC-Machining has extensive equipment and a high degree of automation. WCO covers all of the company’s machine tools except for the sawing machine. In practice, this means:
- Two robot cells for lathes
- Bar-type automatic lathe
- NC center lathe
- Multi-function lathe
- Three horizontal milling machines (in the FMS)
- Reamer
- Planer-type milling machine
- Four 3-axis vertical milling machines
To sum up, WCO enables production control to move towards order-based control, i.e. reduction of batch sizes and more just-in-time production vs. the need to assemble the final product at the customers’ factories. The software enables total optimization of production in a situation where the production involves many manual machine tools or production cells. Fastems’ guiding principle in the development of automation is to make the entire production do the right things at the right time – all the time.
A development-oriented mindset and automation complement each other
Joensuun CNC-Machining’s main idea is the continuous development of operations, in which automation fits perfectly. Herranen quotes Daft Punk: “better, faster, stronger…”, and he continues with an interpretation:
“Never stop. Keep developing. This means that good is not enough – you can always strive for better. For example, our company has achieved the ISO 9001 quality standard and will apply for 14001 in 2021.”
Holopainen agrees:
“If we had been content with the profitably running business before building our own hall and making the FMS and other automation investments, which happened in 2012–2014, we certainly wouldn’t be where we are now. The world and the competition would have passed us by. From this point of view, of course, we are still a long way from the finish line, so the work continues. We are constantly thinking about what to develop next. We have visions, but let’s keep them behind the curtain for now. Multiplying the turnover with the same staff – that sounds like a suitable goal!”
For younger machine shop entrepreneurs who are just starting in business, the experienced Holopainen and Herranen would stress the following lessons: a visionary approach, customer satisfaction, and continuous development are essential for success. Developing the production environment alone is not enough – you must look at the whole operations of the company. On the other hand, balancing between work and leisure is also important. Holopainen sums it up:
“If I could change anything, I would have made more time for my family and taken real vacations. For the last couple of years, I’ve only been doing this, and automation has certainly helped, too. With automation, you can sleep better at night, knowing that things will work out even if a machine breaks down.”
Herranen also recommends personal education.
“I have just started Lean Six Sigma Black Belt training, which provides strong know-how and technical skills for statistical problem-solving.”