Budapest, April 23, 2024 – Siemens Energy in Hungary has selected Fastems as their automation partner in their new and highly integrated manufacturing system at their Budapest factory. Featuring a robotic FMS with automated pallet and cutting tool changes, the flexible automation system answers the growing need to produce high-quality turbine blades and vanes efficiently and safely.
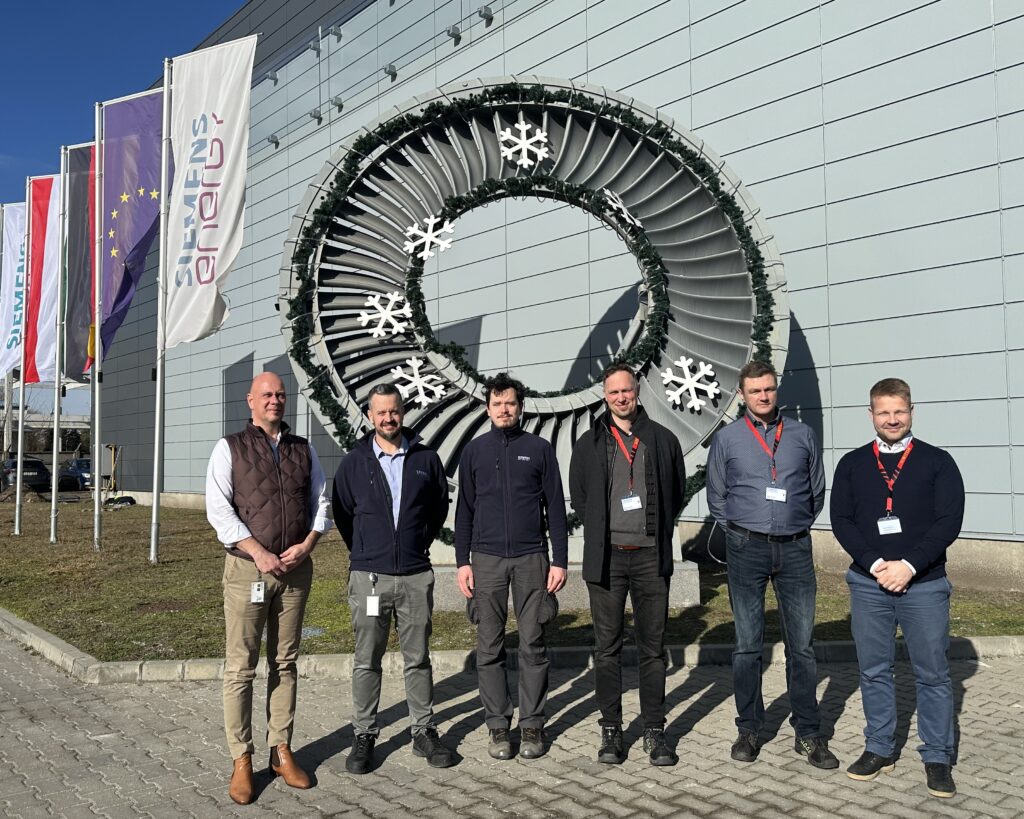
Siemens Energy has an ambitious production development project ongoing in Budapest. One part of the project is to develop a manufacturing system enhancing machining capacity, cutting down lead times and further increasing work safety and ergonomics.
“We want to strengthen our manufacturing competitiveness and offer a workplace that is as safe as possible for our employees. Our customer demand is growing and therefore we need to add more capacity and enable lights-out manufacturing (fully automized production) over weekends. At the same time, we want to improve lead times and ensure top-notch quality. By partnering with Fastems and implementing flexible automation, we can take a huge leap forward in all these aspects,” says Mr. Péter Tállai, Technology Expert at Siemens Energy.
The automation system by Fastems includes RoboFMS (robotic flexible manufacturing system) that integrates two grinding machines, a sink EDM, a washer and a coordinate measuring machine (CMM). The system is integrated with Siemens Energy’s ERP and it schedules and runs production based on customer orders. In addition to automating machining and quality processes, the cutting tool and grinding and dresser wheel transfers to grinding machines are automated with Fastems Gantry Tool Storage (GTS). GTS also ensures that the tool presets are always correct and worn-out tools are automatically brought to tool room. From the operator point of view, work safety and ergonomics is expected to improve significantly with the adjustable loading stations, reduction in manual transfer tasks, and full transparency view on the entire production process via the Manufacturing Management Software MMS.
“We are excited to work with Siemens Energy and be part of this forward-looking project to realize their manufacturing vision at their Hungarian site. High integration level of this system enables manufacturing of high variety of parts efficiently, fast and in high quality. We’ll eliminate unnecessary work-in-process between manufacturing operations and ensure full capacity utilization round the clock,” says Matti Kangas, Head of Business Development of Eastern Europe at Fastems.
Siemens Energy starts production with their new system in 2025. The Budapest manufacturing facility delivers turbine components as part of the company’ global manufacturing and service network. If you want to read more about their products, solutions and services, visit the Siemens Energy webpage.
In case you are interested to learn more about flexible CNC automation, visit fastems.com/offering/automation-systems.
Media contact: Sarianne Niemi, Senior Marketing Manager, sarianne.niemi@fastems.com