Fastems Training – Helping You Reach New Levels of Productivity
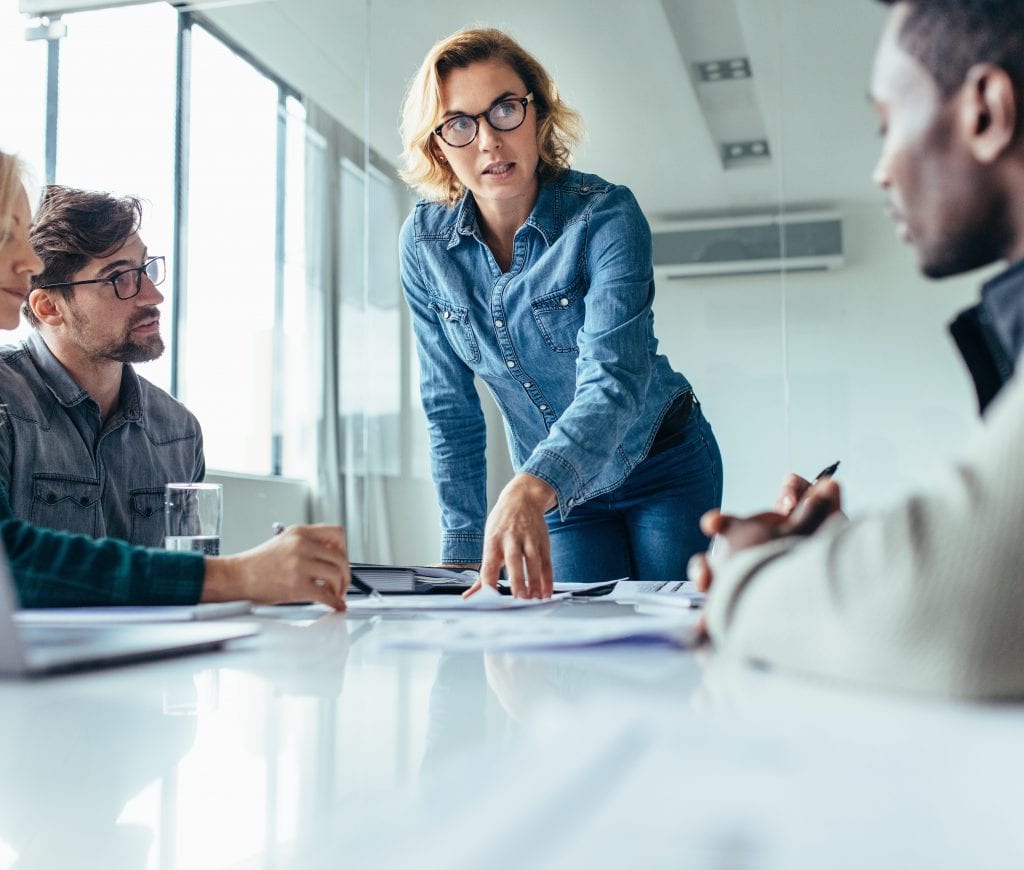
What does Fastems Training have to offer?
The seven most commonly asked questions
1. Why do I need training? Shouldn’t your system be easy to use?
Fastems pays a lot of attention to the user experience of its automation systems. While Fastems Manufacturing Management Software (MMS) features various benefits that can help manufacturing companies improve their productivity, not all functionalities are useful for all companies. That’s why it’s important to train system users properly, so that they can find the best and most productive way to utilize Fastems MMS in their production. There is only one MMS – but many possibilities how to use it!
2. What kind of solutions does Fastems offer customers who want to prepare themselves for a quick and efficient production ramp-up?
Fastems has a wide selection of training solutions, which are targeted towards various MMS user groups. The exact content is defined in the specific training plan together with the customer. Training sessions are spread out over the different delivery phases of the Fastems automation system, enabling the customer to prepare themselves for the arrival the system and the consecutive production ramp-up. The training prior to the system delivery may take place in a virtual environment as well as in the Fastems Training Center located in Tampere, Finland. Both of these training environments can also be used after the system delivery for further in-depth simulations.
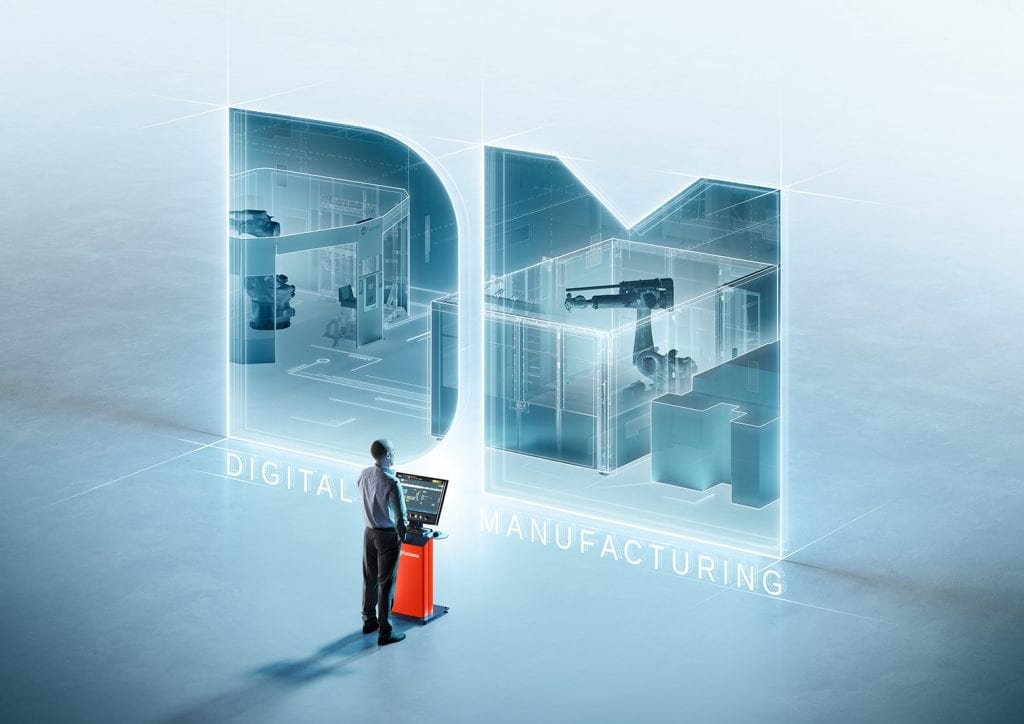
3. What kind of virtual tools do you offer in online training?
We can use Virtual MMS, which runs in the cloud environment and requires no additional hardware. The Virtual MMS configuration can also be adjusted to match the real production system configuration. This keeps training as realistic as possible, regardless of where you are.
4. We feel that we are not utilizing MMS control to its full potential. We don’t know how MMS scheduling could be used in a more efficient way to support our production planning. Can you help us?
When used in the right way, MMS scheduling creates great benefits for production planning. Typically, a system’s users can be split into three groups: operators, production engineers and production planners. All of these groups have different needs, which is why it is important to give the right kind of training for each group.
Fastems offers both standard and customized training packages. These are tailored to support production planning, and to teach personnel, for example, how to add new and edit existing master data and production orders in the MMS.

5. I have a 5 year old Fastems FMS in my factory and the personnel who were originally operating the system are not working at our company anymore. The current personnel feel like they need a refresher on how to best use MMS. How can Fastems help in this case?
6. We would like to improve our maintenance team’s troubleshooting skills for our Fastems system. Can you help us?
Fastems also has courses tailored for maintenance personnel needs. To give you an idea, examples of the course topics include basic troubleshooting, recovery from errors, and system parametrization using the MMS Service Tool. You can contact your local Fastems service manager to create a customized training package.
7. What other features might I add to my systems, as my needs and needs of my customers change?
Over 50% of delivered Fastems systems are somehow modified or extended within three years after ramp-up. The modifications can consist of hardware changes (adding more machines, loading stations etc.) or software upgrades. Fastems MMS software functionalities consist of software modules that can be added to the system also later when needed. Some examples of the MMS software modules include ERP-interface, machine status monitoring, MMS Dashboard and production document management. Most of the software modules can be installed remotely but some require Fastems software specialist visit.
Contact your local Fastems representative to hear more about MMS upgrades.
Where can I find additional information?
Interested to learn more? Check out an overview of our Life Cycle Services or simply leave your contact information below. We’re happy to walk you through the different options available for increasing your productivity.
Interested in hearing more about Fastems Training and Life Cycle Services?
Fill in the contact form and we will get in touch.
"*" indicates required fields