Wood Processing Equipment Leader Achieves Consistent and Efficient Throughput For with Software Maintenance Agreement
Woodland, WA – USNR is a world leader in the building and maintenance of sawmill and wood processing equipment. Their Woodland, Washington, location specializes in the machinery components that go into the impressive equipment units that cut, shape, plane, and chip wood.
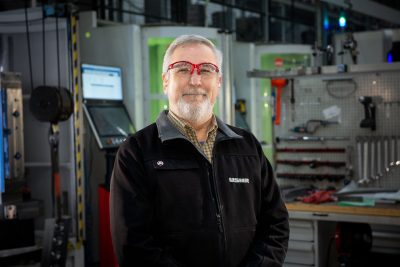
Operations Manager Mike Smothers has one less thing to worry about with the adoption of the MMS Maintenance Program which helps keep his entire shop floor running smoothly.
Operations manager Mike Smothers calls the Woodland shop a “high mix, low volume” manufacturing center that produces difficult-to-manufacture parts for high-speed saws, chippers, and profilers. Most parts are produced in runs of twos or threes. The machines that USNR manufacturers are made to order. Because of this, much of his production time has been spent setting up, retooling, or tearing down a run.
In 2019, Smothers installed the Fastems Flexible Manufacturing System ONE (FMS) to streamline and simplify his manufacturing processes. The modular pallet automation system connected three DMGMORI NHX 6300 horizontal machining centers with a 54-pallet pool for smoother material management. Each machining unit was equipped with identical resident tooling so that they each could be completely independent production elements. The FMS took setup completely offline so that material and tools could be mounted unmanned
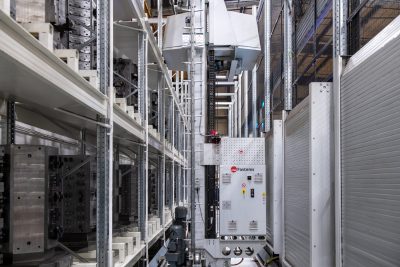
The FMS connected with the shop’s Kardex Remstar vertical lift storage units. Its installation took Woodland’s average delivery time from 25 days down to nine.
“The FMS allowed us to replace all of our standalone machines with units that can run spindles almost continuously without worrying about setups,” said Smothers. The FMS is connected to the shop’s Kardex Remstar vertical lift storage units, which held and organized stock materials, parts, fixtures, and tooling for easy access. Its installation took Woodland’s average delivery time from 25 days down to nine.
The FMS is powered by Fastems’ advanced Manufacturing Management Software (MMS). USNR is running Version 8 which collects data from various points around the shop, calculates, and provides meaningful insights . Users can automatically generate production plans, track materials and tools, monitor production in real-time, view key performance indicators, and more. “It’s vital for operating our system and knowing where we’re at and what we’re doing. It even helps with scheduling,” said Smothers.
MMS data can be accessed by anyone multiple times a day most often by glancing at the Dashboard as they walk by. The team can view spindle utilization rates, machine capacities, and cell use within seconds. Smothers creates daily reports on what and how things were done so that his team can see the utilization and throughput easily.
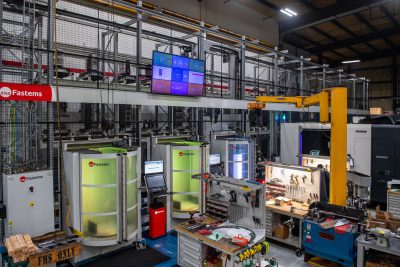
Every member of the team can access the Manufacturing Management Software multiple times a day, often just by glancing at the Dashboard as they walk by. Within seconds, they can see spindle utilization rates, machine capacities, and cell use.
A 2021 merger with Burton Mill Solutions, a manufacturer of products for maintaining and sharpening wood processing equipment, found USNR with two facilities with the software in place: the Woodland location and Plessisville, Quebec. Woodland currently produces approximately 7,000 pieces a month. Plessisville, with its 5-axis Okuma unit produces larger components with longer run times and less volume than the Woodland facility. Smothers is adamant about keeping both facilities – as well as any future facilities that adopt FMS – with the latest version of the MMS . “The bottom line is that this software is the brains of your whole system, so you want it to be functional, up to date, and easy to use,” he said.
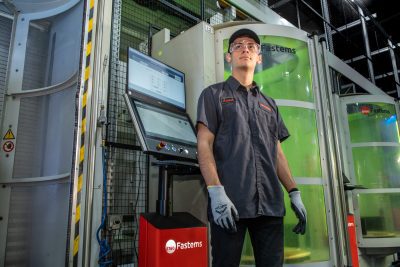
USNR’s MMS V8 Maintenance program is designed to provide the shop with technical support, training, and automatic updates to the latest MMS modules for best possible production outcomes.
Smothers approached Fastems with the idea of a Maintenance Program for his MMS 8.0, and adopted the Software Maintenance Agreement with the aim to provide the shop with technical support, training, and automatic updates to the latest MMS modules for best possible production outcomes. Keeping the software up-to-date and running well is crucial. “If our FMS or MMS goes down, we’re dead,” Smothers said. The cost of the maintenance plan is nowhere near the cost of his system going down. With the Software Maintenance Agreement in place, new releases are automatically installed over the web, and Fastems can also send out experts to the USNR shop to troubleshoot and train onsite as needed. With two facilities in two different locations running simultaneously, the ability to access remote support when things go awry is critical. Consistency in both locations is key to minimizing downtime in between runs or when new equipment is added. Smothers keeps back-up hard drives just in case of major crash, all of which are maintained to the newest version as well.
The option to update from year to year, or how to utilize Fastems’ training and service, is entirely up to USNR as they can choose when they want to have the updates installed. Whenever that is, and no matter how long it takes (depending on the size and variety of Fastems’ systems at the customer’s site, software updates take up anywhere from a couple of hours to a few days before all functionalities are verified), they can be sure there will be no production stops during the installations. The adoption of the Maintenance Agreement has taken one load off of Smothers’ back, allowing him to focus on the other important aspects of his job, all of which demand a good chunk of his time.
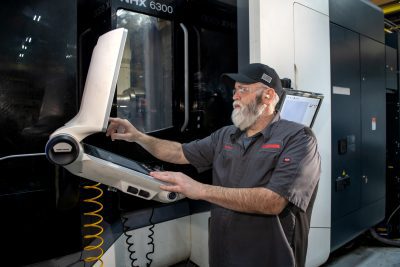
The Fastems Flexible Manufacturing System ONE modular pallet automation system connects three DMGMORI NHX 6300 horizontal machining centers with a 54-pallet pool for streamlined material management.
USNR recently merged with Wood Fiber Group. “With the merger we have transitioned parts from our new sister company to our FMS,” said Smothers. “This transition has gone smoothly, and we have produced over 200 different parts in six months.” The FMS has helped with bringing on new products without disrupting the rest of the shop or the system. The continuous maintenance and updates to the MMS will help manage the cell and how well it functions for now and in the future.