A revolutionary business model needs revolutionary automation
this article is A SUMMARY. see original from the mtdcnc magazine 11/2023, pages 28-30
Rodin Machining is a Dutch contract manufacturer, offering an online portal for their customers to order parts with. Thanks to AI, quoting takes less than a minute and manufacturing can start almost immediately. Fastems’ automation runs the factory, making the high-mix manufacturing of Rodin both flexible and efficient:
“We’ve created this autonomous factory together with Fastems. We are delighted to have teamed up with them and we are pushing each other to the next level”
About Rodin Machining
Rodin Machining is located in Opmeer, circa 45 min drive from Amsterdam, and it works with variety of clients from machine building to construction, furniture, automotive and petrochemical industries. The company was founded Ruud Appel, Gem Bot, Dennis Oud and Paul Mooij who are experienced in the sheet metal industry and software and data engineering. The company is named after the famous sculpturer Auguste Rodin. Ruud, Gem, Paul and Dennis explain their unique business model:
“Customers can upload their 3D design and a PDF file with the tolerances 24/7 and then select material type, quantity and delivery date. A quotation will be delivered in 30 seconds. Upon quotation approval, automated manufacturing starts immediately: your project is put into the ERP system and as automated as possible turned into machine and robotics programs by the CAM engineers. There are limitations on part sizes, and we typically produce volumes from tens to thousands – but that is it. We are not about shaving seconds off volume production, but creating a steady high-mix flow that will run 24/7 unmanned. While a typical CNC machine runs 1500 to 2000 hours a year, the FASTEMS logo says ‘8760’ referring to the yearly hours – and that is where we want to be with our spindle hours.”
We have to have human interaction while creating the CAM file, loading/unloading the system and also pre-setting the cutting tools, but more than 90% of the process is automated.”
Great partners make great cooperation
The idea for Rodin Machining was born in late 2021 and everything began with a search for the right partners. As the scope of automation became clear, Fastems was the obvious choice. Without a customer base or a factory to work from, the four entrepreneurs decided to take the ‘leap-of-faith’ and a futuristic flexible manufacturing system was delivered in Opmeer during 2023. Ruud goes on explaining their approach:
“We wanted to create an autonomous factory without people and only robots. Everyone told us that it wasn’t possible, but we wanted to stretch the bounds of what was possible. So, we started gathering a group of leading suppliers like Fastems in CNC automation and asked them searching questions – ‘Have you thought about doing it like this?’ and ‘Why do you always do it like that?’. We wanted to know why everybody thought that historical processes were the only way to proceed. We really wanted to change the mindset.”
Rodin’s team had very high requirements for the project, especially around automation and integrations:
“We needed machines that were as versatile as possible and we needed Fastems to create the integrations and automation with cutting tools, tool data, workholding, grippers, chucks and software like ERP and CAD/CAM. Rodin and Fastems worked together to calculate how to get the most machines into the factory space and create the optimal workflow. There were many iterations and when we were settled upon a final design layout, we set about building the factory and teamed up with our partners to realise the project.”
Paul Mooij explains the mindset and also comedy around the project:
“Along the way, we were met with a lot of ‘you can’t do that’, ‘that is not possible’ and ‘it’s always been done like that’. Our team and our partners agreed that every time we heard those negative phrases, the perpetrator would have to buy the drinks. A lot of people bought beers – which usually yielded solutions, and we managed to change the mindset and have the project delivered.
How the system works?
The system handles cylinder and prismatic parts. Both raw materials and ready parts are kept in the central storage. The cylinder part raw materials are delivered on a pallet by a crane and are processed by a robot cell serving two Mazak Integrex turning machines. With prismatic parts, a robotic autoloading cell is used to load the raw material into a smart fixture, attached to a zero-point plate which is carried by another robot to the table of Mazak Variaxis machine. Ready parts are similarly handled by the autoloading robot and returned to the central storage, which is used used for material input/output. The system also features a station for AGV-based tool delivery from the tool room. Both milling and turning side of the system feature automated tool changes, including delivering tool-offset directly to machines. For more detailed system specifications, see the system configuration section below.
Once parts are programmed with CAM software, they are dropped into the Fastems Manufacturing Management Software (MMS) that will automatically generate a production plan based on order due dates, inventory balance or recurring batch runs to ensure the timely delivery of parts. The MMS forecasts the optimised production workflow, days in advance by preparing resources to minimize machine waiting times and WIP. The MMS also provides real-time production monitoring, tracking key performance indicators from OEE, machine tool utilisation and available resources.
Outcome
The system enables unmanned high-mix production in advanced milling and turning applications. This means easy and unmanned introduction of new production parts, including automated set-up changes both in milling and turning. Tool delivery and data transfer are automated, too, including delivering offset data. Fastems MMS control act as production brains, automating production planning and scheduling. The outcome is high machine utilization combined with just-in-time production capacity, fast lead times and situational awareness.
System Configuration
Overview:
- Up to six Mazak Variaxis 5-axis milling machines supported by an autoloading cell
- Up to six Mazak Integrex turn-mill machines supported by robot cell(s).
- Material storage in the middle for raw materials and both milled and turned parts
- Both milling and turning cells feature automatic tool handling, including the delivery of off-set data to machines.
- AGV tool delivery option
Milling side
Turning side
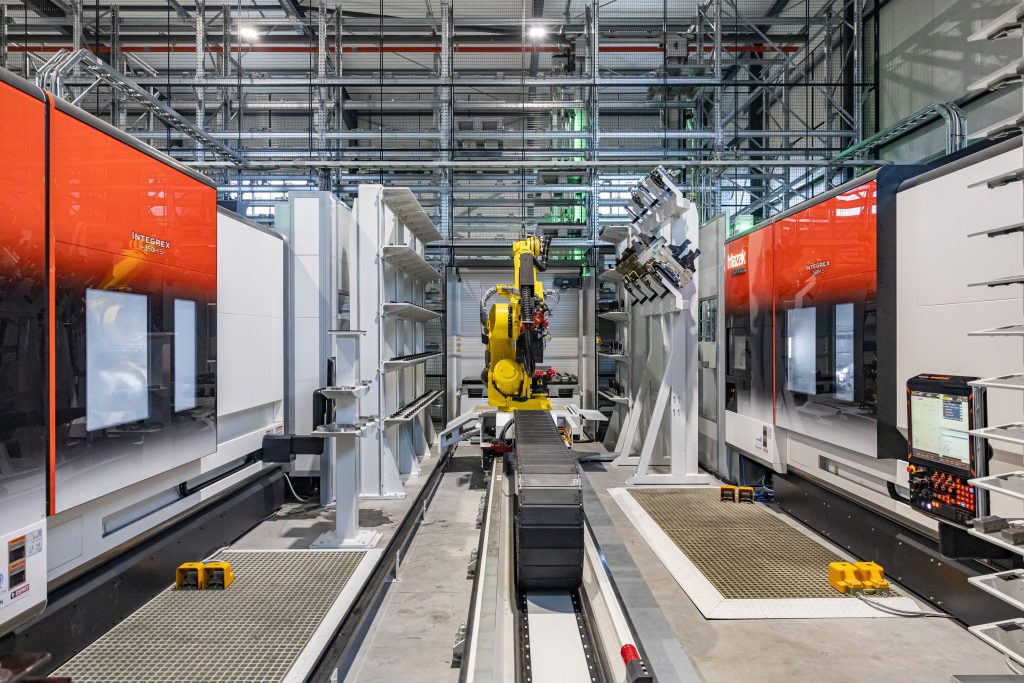
Agile Manufacturing Cell
- One robot serves two Mazak turn-mill machines.
- Set-up changes happen by changing the chuck.
- Tool change by the robot via magazine door.
- Robot uses different grippers for workpieces, tools and chuck changes
- Chuck jaws can be machined per need when introducing new parts
Outcomes
- Autonomous turn-mill manufacturing
- Automated hard & soft jaw handling
- Automated part handling
- Automated tool & tool data handling
- Automated production planning and scheduling
- Just-in-time production
- Situational awareness
- Fast lead times
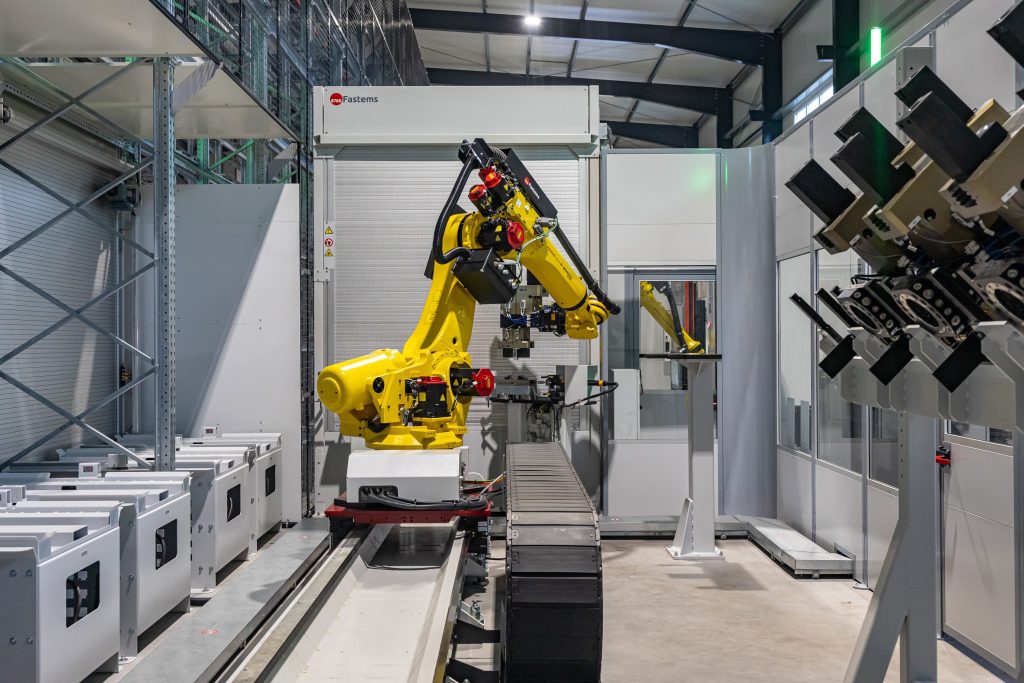
Autoloading Cell
- Material input/output via high-bay storage
- The robot attaches a workpiece to a universal smart fixture and back
- Robot programs are automatically delivered to the robot
Outcomes
- Autonomous part handling
- Automated stock material loading from pallet station into vice
- Automated regripping – from OP10 to OP20
- Automated ready part unloading from vice to pallet station
- Automated production planning and scheduling
- Just-in-time production
- Situational awareness
- Fast lead times
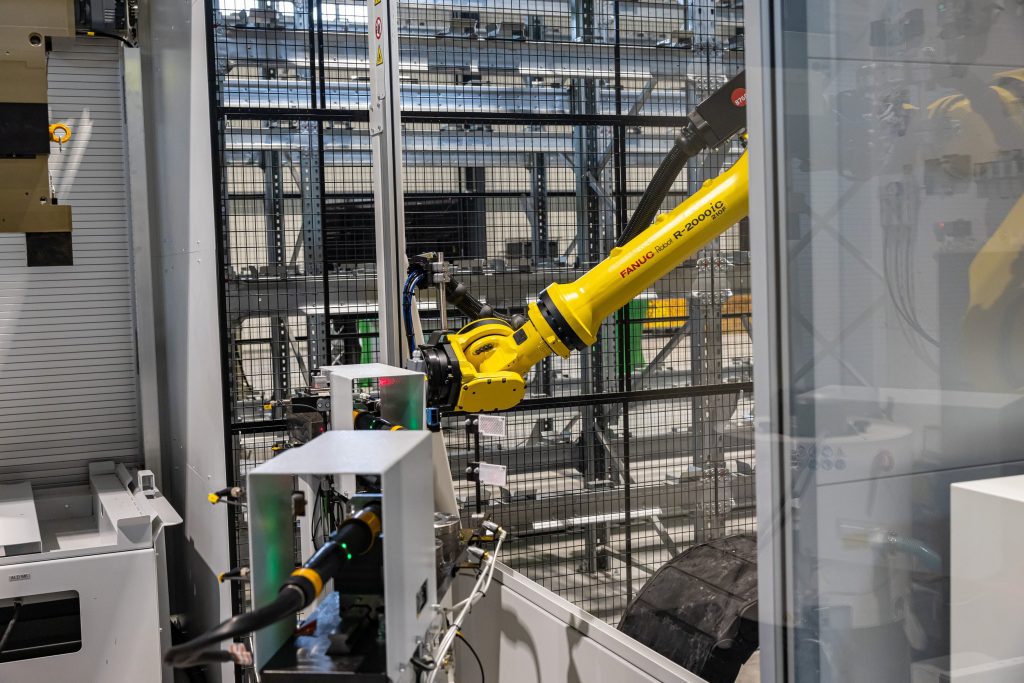
Robotic FMS
- Robot serves up to six Mazak 5-axis milling machines
- Zero-point plate delivery to the machine table
- Tool changes via magazine door
- Small buffer for flexibility
- Material input and output via autoloading cell, option for AGV tool management
Outcomes
- Autonomous 5-axis milling manufacturing
- Automated pallet handling
- Minimum (un)loading time, maximum machining time
- Automated tool & tool data handling
- Automated production planning and scheduling
- Just-in-time production
- Situational awareness
- Fast lead times
Want to hear more? Give us a call or an email!
"*" indicates required fields