Learning Flexible Automation at Race Car Speed
As part of an internal “Formula 1 project,” Cutmetall Recycling Tools Germany set out to gain practical insights into automation in record time. The goal was to develop and test new production standards, workflows, fixtures, and NC programs that could be directly transferred into a larger Fastems system by 2025. In doing so, Cutmetall laid the groundwork for a fast and low-risk ramp-up of a multi-machine automation system.
Headquartered in Eisfeld, Thuringia, Cutmetall Recycling Tools Germany is part of the Cutmetall Group and operates as an OEM with around 40 employees. The company manufactures wear and replacement parts for the recycling industry. “We produce batch sizes ranging from 1 to 20,000, though the average range is between 20 and 200 parts,” explains Managing Director Florian Fischer.
Only Spindle Hours Generate Profit
Fischer has a very distinct view on automation. When asked how he would assess the automation level at his facility prior to the Formula 1 project, his answer was clear: “It depends on what you mean by automation. We have 12 CNC machines, one sawing center, and three robots for machine loading and unloading. That might look high-end to some – to me, it doesn’t. From a Lean Manufacturing standpoint, there’s still too little distinction between value creation and waste. Automation should never be about just keeping things running. It’s about maximizing spindle hours – that’s where the profit comes from.”
Learning Fast from Real-Life Automation
According to Fischer, the shortage of skilled workers is the biggest constraint on Cutmetall’s production capacity. “We also lacked equipment that could run lights-out, and until now, we didn’t have a single horizontal machining center. Even on vertical machines, chip evacuation is the main bottleneck, making 24/7 production difficult. On top of that, our machines didn’t have large enough tool magazines.”
To change that, Fischer and co-owner Oliver Huther launched the Formula 1 project – with the ambition to prepare for a future Fastems Multi-Level System (MLS) that would link multiple CNC machines in a flexible manufacturing system. The first step: implement a compact automation solution quickly and collect valuable hands-on experience.
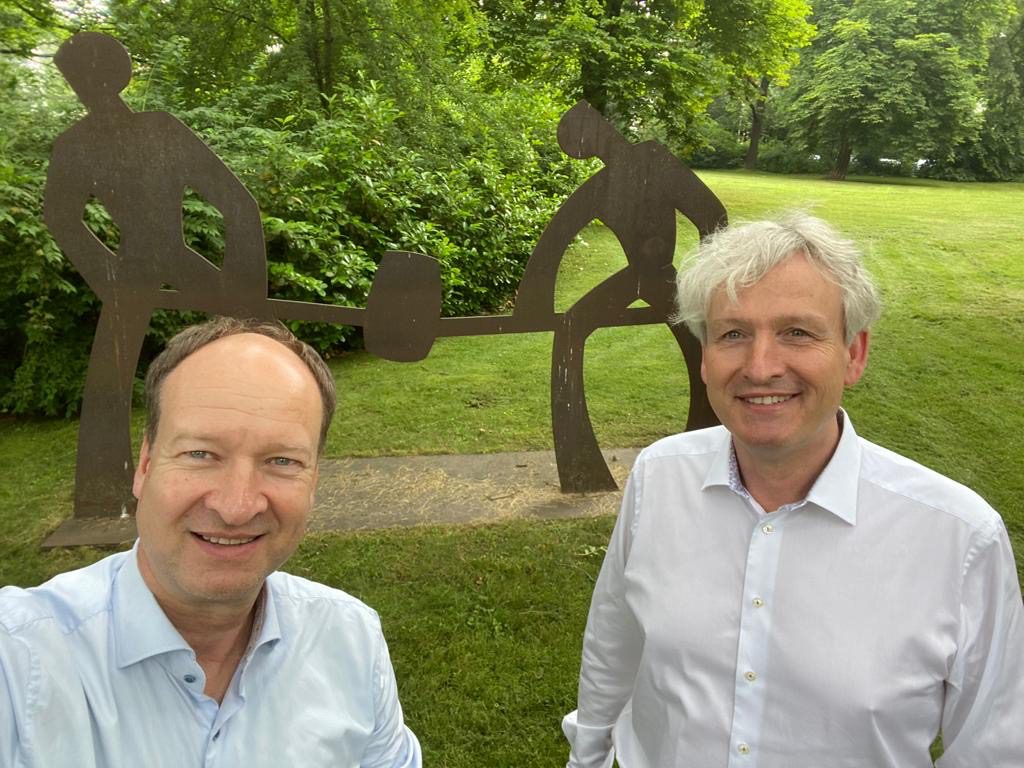
Standardize First – Building Foundation for Productivity
To support this transition, Cutmetall began systematically standardizing its production environment:
- Investments are now limited to machines with uniform controls, pallet changers, and clamping systems,
- Only horizontal machining centres with automated chip evacuation will be used,
- Coolant/lubricant management will be automated as well.
Fischer defines the main goal as follows: “All setup, changeover, tool handling, and chip removal processes must happen in parallel with the machining time.”
To evaluate potential automation partners, Fischer visited many companies across the region – aiming to learn from other people’s mistakes before making their own.
Fast Progress: From AMB Trade Show to Productive System
Cutmetall first encountered the HF 5500 horizontal 5-axis machining center by Heller at AMB 2022. On the Fastems booth, they discovered the Flexible Pallet Tower (FPT) – the missing piece to complete their solution.
“Shortly after the show, we bought the machining center directly from Heller’s production line, along with the FPT-1000 from Fastems and a pre-setting device from Haimer,” says Fischer. “We aimed to have the entire system up and running, fully integrated and productive by April 2023.”
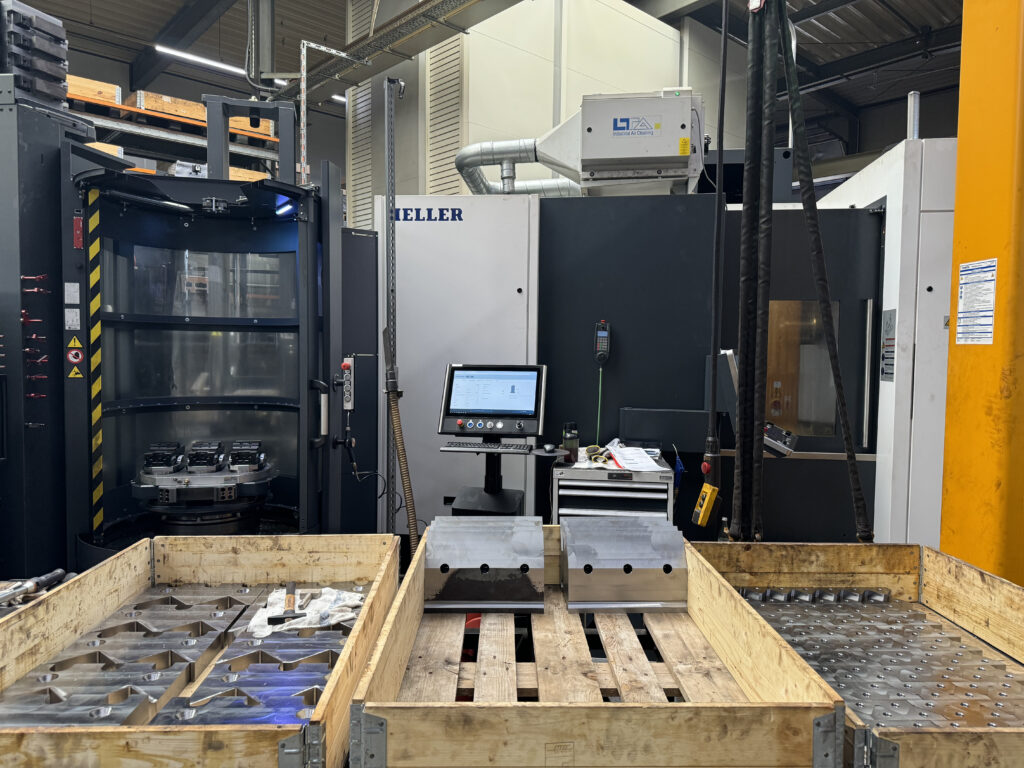
What convinced Fischer most was the space-saving concept of the FPT-1000, which enables high pallet capacity in a compact footprint. Designed for payloads up to 1,500 kg (including pallet) and pallet sizes between 500×500 mm and 630×630 mm, the system can store 12–24 pallets in two different heights – all in just 19 m² of floor space. This setup supports highly productive, order-driven manufacturing with a single CNC machine.
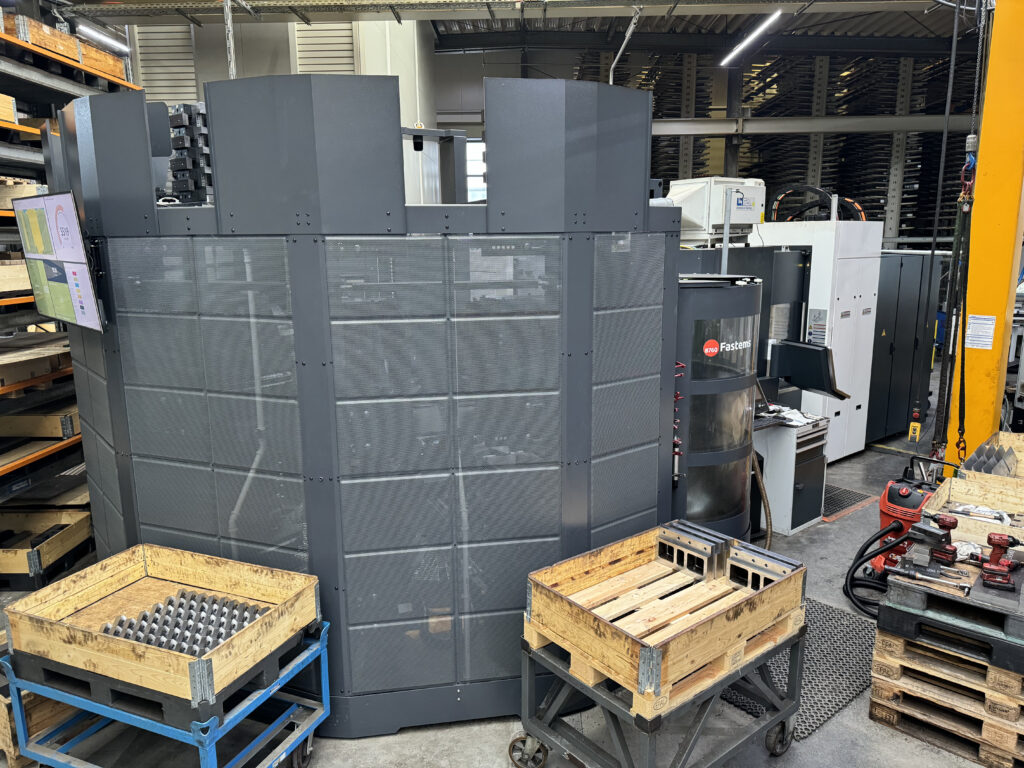
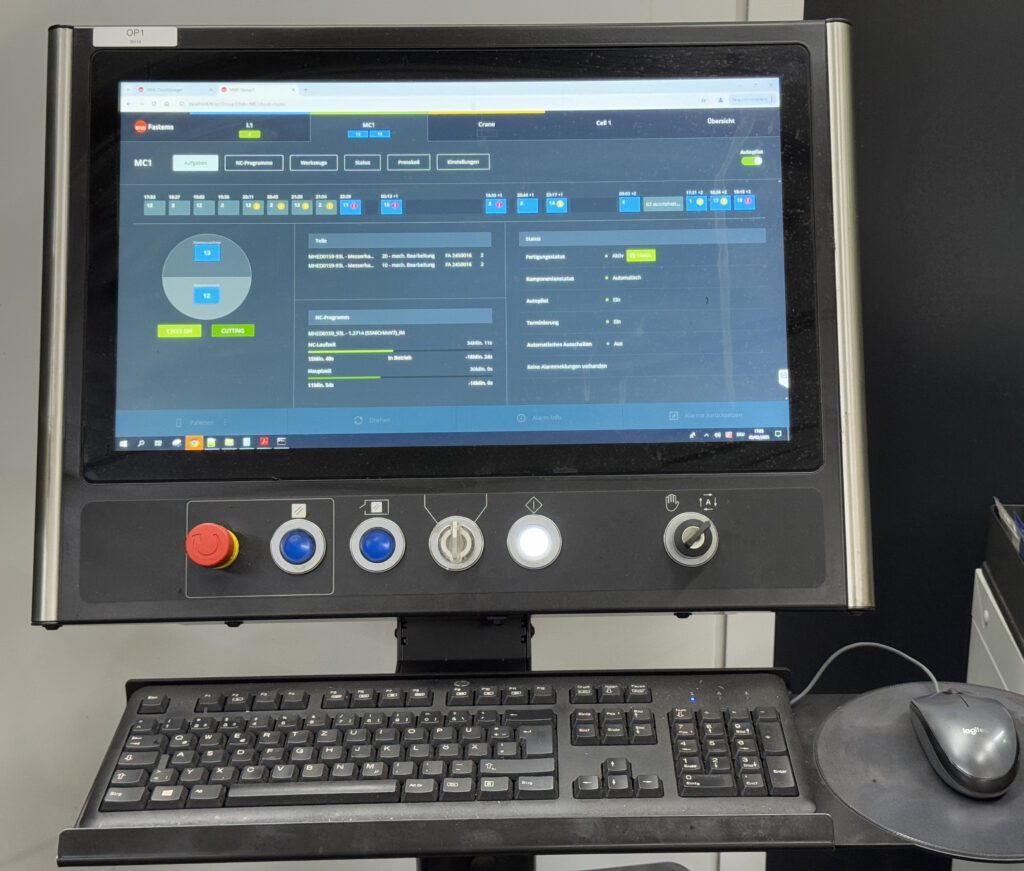
Software Makes the Difference
For Fischer, it wasn’t just the hardware that sealed the deal – it was the overall system integration, especially the software. “The control software interfaces between the machine, the pre-setting device, and the automation are absolutely critical. Fastems MMS (Manufacturing Management Software) ultimately tipped the scales in favour of Fastems.”
MMS is one of the most advanced software solutions for automated production planning, execution, and monitoring. It can schedule manufacturing operations up to 96 hours ahead. Most importantly, it focuses on resource readiness: “Before a job is launched, MMS checks for material availability, NC programs, tooling (including remaining tool life), fixtures, and more. Only once everything is ready does the system begin production. As a result, we have far fewer parts waiting idle between operations.”
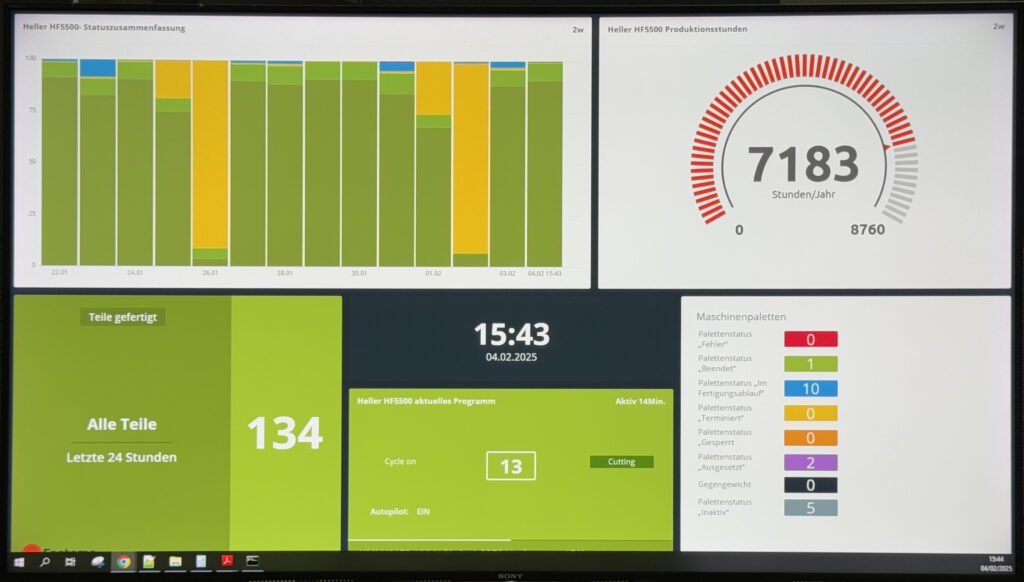
Centrally Managed Manufacturing Resources
Once part data is stored in MMS, repeating orders can be launched immediately. “It saves us a huge amount of time – as long as the raw materials, pallets, and tools are ready,” explains Fischer. “MMS also handles full tool management and sends instructions to the pre-setting device. In that way, all our critical production resources are centrally managed.”
He adds: “Yes, the software doesn’t cut metal – but it significantly increases spindle hours. Every minute a machine isn’t making chips is waste.”
Currently, production orders are still manually entered into MMS. But the future integration of MMS into the ERP system is under planning – the 20 employees in the F1 team are now gaining valuable hands-on experience with the software and its potential.
Keeping Parts Flowing with FPT-1000
Today, FPT-1000 at Cutmetall holds 18 pallets of varying heights. Fixtures stay on the machine pallets, and each pallet typically holds a single part type. After OP10, parts are re-clamped on the same pallet for OP20.
“When a pallet returns from FPT, we always have a mix of finished parts, raw parts ready for OP10, and parts clamped for OP20,” Fischer explains. “Pallet machining times range between 30 and 90 minutes.”
The setup runs in two shifts per day, with an additional unmanned night shift. To support that, Cutmetall is planning to automatically transfer chips from all machines to a central container.
Strong Results and Clear Next Steps
With the F1 project, Cutmetall has already achieved its initial goals: to gain practical automation experience, build internal knowledge, and prepare for the next automation level.
Thanks to the FPT-1000 solution, the company now reaches over 7,000 automation hours per year – of which 90% are actual spindle hours, and only 10% used for pallet and tool changes.
“For a medium-sized company like ours, with relatively small batch sizes, major investments must pay off. The fact that we can now amortize a machine over more than 7,000 productive hours per year is a huge success.”